How to adapt automation to customise mass production
Tekniker is currently leading the ADAPTA project aimed at designing and developing AI solutions which, once incorporated to robotic systems, will make it possible to automate tasks related to logistics, maintenance and assemblage.
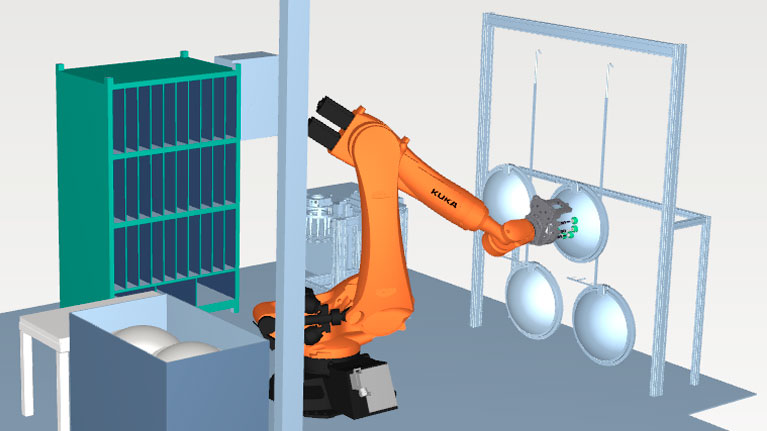
Mass customization is a business strategy that allows companies to adapt their offers to customers and meet their specific needs whilst minimising costs and maximising efficiency. In a nutshell, it’s all about creating unique products or services for each customer.
As this trend has brought about a constant and rapid evolution in many sectors, it is becoming increasingly difficult to incorporate the conventional automation strategies already used in the automotive business or in the capital goods sector as both require sizeable investments and a long time to recover.
Tekniker, a member of the Basque Research and Technology Alliance, is leading the ADAPTA research project funded by the TransMisiones programme sponsored by the Spanish Government to address the challenge of finding an alternative automation system for manufacturers encountering production variability in order to increase their production levels.
The main goal of this initiative consists in designing and implementing a resilient and configurable production model so factories may fully adapt to changes in the environment and do so with total resilience.
Consequently, the project will mainly focus on improving the perception capabilities of robotic systems currently in use by incorporating vision-based solutions, AI, integrated sensors plus 2D and 3D images.
Throughout this initiative, efforts will be made to develop handling systems to adapt to unknown or changing situations with minimal human presence and enhanced interactions to provide a collaborative production environment.
As the organisation in charge of scientific matters, Tekniker will develop AI models to recognise spaces, identify objects and deploy handling solutions based on models generating gripping points automatically.
Demonstration learning techniques will be used, moreover, to speed up the definition of assembly and handling tasks and to shorten programming stages; digital infrastructures will be set up to further interoperability, to foster secure and sovereign data sharing and to enhance life cycle management of automatic learning systems.
Validation in an industrial scenario
The methodology proposed by the ADAPTA project includes the validation of results obtained in an industrial scenario to be provided by Schréder, one of the project partners, at the company’s lamp assembly plant situated in the province of Guadalajara where about 50% of the multinational group’s worldwide production is based.
More specifically, three representative cases related to handling, assembly and logistics in multiple production scenarios will be tested: the loading and unloading of products on the paint line, the collaborative assembly line and the autonomous system used to load finished products on trucks.
With funding provided by the TransMisiones programme of the Ministry of Science, Innovation and Universities of the Spanish Government, the ADAPTA project features a consortium coordinated by Tekniker and made up of Smarttech, CT Ingenieros de Catalunya Aeronáuticos, de Automoción e Industriales, Automatización de Sistemas y Aplicaciones Industriales (ASAI), División Industrial Artisteril, Bcnvision, Schréder Socelec, Eurecat and the Carlos III University of Madrid.