Industry 4.0: enabling technologies for smart machines
IK4-TEKNIKER will show its new developments to face the challenges posed by industrial digitalisation for new machines and the fleet of installed units at the International Machine Tool Exhibition (Bilbao Exhibition Centre, hall 1, stand C22).
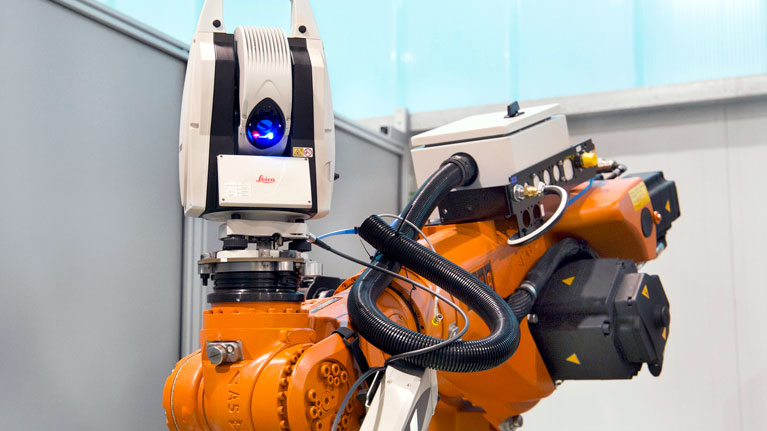
The progressive implementation of Industry 4.0 and digital technologies in the machine tool sector poses challenges such as the ever-increasing quality requirements, more demanding accuracy standards and the introduction of automated, interconnected systems capable of autonomous operation.
The IK4-TEKNIKER Basque Country Technological Centre is working on a series of highly innovative technologies aimed at both new smart machines and the addition of innovative applications that enable digitalised manufacturing environments to already installed machines.
These developments comprise part of the technological offer that IK4-TEKNIKER will take to the next edition of the Spanish Machine Tool Biennial (pavilion 1, stand C22) scheduled to take place from May 28 to June 1 at the Bilbao Exhibition Centre.
The technology centre will present a proposal with technological value that also seeks to respond to the new demands of the sector and opens up new and interesting perspectives from the technological point of view. Having a reference model for diagnosis and identification of opportunities in the field of Industry 4.0 within the framework of the machine tool sector provides a good yardstick to structure the answer to the question "what could make my company more competitive and what performance must such a machine provide?"
This model is an adaptation of the Industry 4.0 general model machine tool used by IK4-TEKNIKER for diagnosis and identification of opportunities in the Industry 4.0 field.
The following sections describe the most important enabling technologies designed to help the machine tool user:
Flexibility and pre-configurability Flexible robotics
The first task in a machining process is loading the workpiece onto the selected machine tool. This job is usually done by hand and systems specific to the characteristics of the workpiece must be designed and constructed if it is automated. That is why loading systems are extremely inflexible and very difficult to reconfigure.
Now IK4-TEKNIKER can offer a comprehensive solution (bin picking, computer vision, path creation, force control, etc.) that enables companies to boost their machines’ productivity and reduce the cost of these - usually manual - loading and unloading phases.
The solution is aimed at companies that machine workpieces in machining centres and flexible manufacturing cells.
Virtual machine: Process-machine modelling and simulation
The aim is to comprehensively investigate simulation technologies (of machines and processes), monitor and analyse data to configure a hybrid, streamlined performance modelling platform that enables machine manufacturers and, in particular, users to drastically optimise their design processes (in time and cost), ramp-up, production life cycle and adaptation to new requirements while increasing their quality and reliability ratios.
Health assessment
Sensorisation of the machines in an efficient, distributed and comprehensive manner by means of multi-variable monitoring devices enables continuous access to real-time information on the performance of their components, the status of the production processes, quality parameters of the workpieces being manufactured and the variable environment in which production is taking place.
IK4-TEKNIKER proposes a series of very simple, rapid tests of the machines to ascertain their status and condition by means of the variation over time of a series of parameters based on the readings obtained by the external and internal sensors. IK4-TEKNIKER calls this the machine’s “fingerprint”.
This process provides knowledge of how the machine is working and monitors the unit’s health in a controlled manner.
It enables operators to be aware of the machine’s health status when making decisions that affect operation and maintenance. It also enables prior knowledge of geometric errors in the workpieces, thus taking a step towards “zero defect” manufacturing - a vital aspect especially in the case of expensive pieces.
Optimising the process
Until now, theoretical simulation models analysed the machine tool and the machining process independently, without the slightest interaction between the two.
Platforms are now being developed on which various simulation models are integrated to comprehensively analyse the machine’s operation and its machining processes. This technology ushers in a new simulation concept that includes both the process and the machine itself.
Moreover, the simulation models were used in the design phase as predictive models to obtain information before performing the actual task. However, we have currently made a significant leap forward and now the results can be used to perform online control during machining.
We have developed multi-objective optimisation strategies with the result that the machines themselves are able to make decisions autonomously and intelligently involving the process parameters and the dynamic conditions of the mechanical components which ensure, in each case, that the production objectives set are reached (costs, production, energy consumption, machine status, etc.) on the basis of the data harvested in real time and of the established models and patterns. This process will ensure optimisation of the manufacturing processes.
Fleet management: Progressing from a machine to fleet management
The first step is to sensorise and monitor the machines using the simulation models of both the machine and the process, all working in a coordinated manner (in closed loop) and enriched with the "fingerprint" tests. These enable us to optimise the processes and ascertain the health status of the machine’s components.
Once this important step has been taken, the next is to know the health status of all the machines involved in the production line.
A benchmark in metrology and inspection
As the volume of a machine tool increases, verification of the geometry of these systems becomes more and more complex. In this scenario, the use of traditional verification technologies such as interferometry or electronic levels are no longer useful since they do not ensure the high precision demanded by high-requirement sectors such as aeronautics.
Therefore, to ensure the geometry and operability of its machine tools, IK4-TEKNIKER works with the multilateration technique to develop a procedure that enables geometrical measurement of a machine tool across its entire working volume in a shorter time, automatically and more accurately than is possible using current technologies. Specifically, the Basque Country Technology Centre has completed the technological development with the use of a laser tracker located on a mechatronic system. This development is currently pending award of the patent.
Industry 4.0 + Inspection and metrics = Automatic, built-in verification of the machine
The system also enables easy detection of small differences in the behaviour of the machine over long periods of time and reduction of its thermal drift.
It will be possible to see a real application of this solution in the exhibition area of the Technology Centre at the Biennial Exhibition.