Printed flexible electronics to help space missions lose weight
Tekniker is leading a European Space Agency (ESA) project aimed at developing, manufacturing, testing and validating printed structural electronics to be used in outer space.
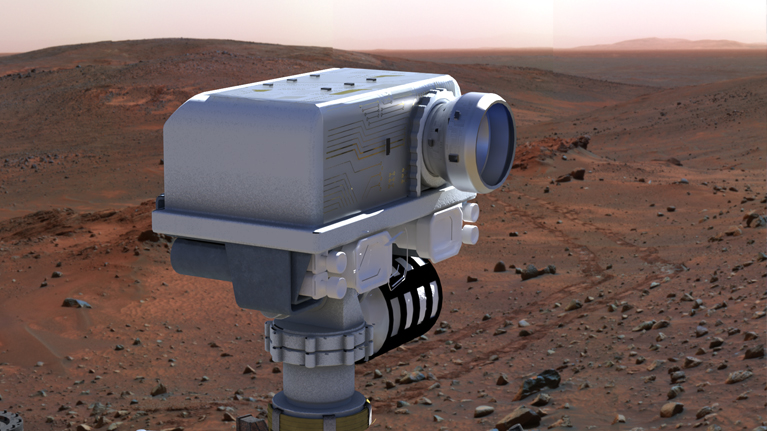
The possibility of directly integrating printed circuit boards and electronic assemblies on mechanisms and structures thanks to printing and thermoforming technologies offers an extensive range of options in different sectors such as household appliances or the automotive business where they are increasingly being used, for example, on car instrument dashboards.
These new solutions are rapidly changing how electronic functionalities are manufactured and integrated in different kinds of instruments or components to be tested for the first time ever in Europe in space applications under the umbrella of a new project funded by the European Space Agency (ESA) and led by Tekniker, the Basque technology centre.
The main challenge posed by the Printed Structural Electronics (SIPRES) initiative will consist in developing, manufacturing and validating the use of flexible, printed and hybrid electronics on several prototypes that can operate correctly under extreme conditions of temperature, vacuum and radiation as required by space research and exploration missions.
Borja Pozo, the coordinator of the Space Sector at Tekniker, explains that “this project is highly innovative as it is the first time that ESA will run experiments by applying electronic systems printed on flexible materials for use in space”.
“The expert also states that “the weight of the devices and elements launched into space is a crucial and determining factor for the success of a space mission. Thanks to this technology, characterised by less material and reduced weight, future missions will cost less and be more sustainable. In the case of many components and surfaces, it will be easier to integrate electronic capabilities regardless of their shape”.
Fine-tuning prototypes
Tekniker will contribute its know-how and expertise in electronics, manufacturing, surface chemistry and coating technologies throughout the entire fine-tuning of prototypes from the moment of their inception until they are technologically developed and close to being introduced in the space sector.
The engineering firms ALTER TECHNOLOGY and CT Ingenieros - Cadtech will also play a role in this process to test and validate a range of polymeric materials, inks, conductive adhesives and manufacturing processes to check their compatibility with the required environmental conditions and electronic space components.
The printing of electronic assemblies and devices will be carried out at Tekniker’s 3D printing lab.
Once fully developed, tested and validated, it will be possible to commission the first technological demonstrators aboard nanosatellites used for Low Earth Orbit (LEO) research or verify testing campaigns for the International Space Station (ISS).
In parallel, and based on a roadmap devised by ESA, it could be possible to address final prototypes for future missions to the Moon and Mars.
The Tekniker expert also adds that “among the range of potential solutions that can be developed thanks to this this technology we can find the integration of wind and humidity sensors for rovers on Mars; radiation and temperature sensors and photodetectors for Moon operations; power sensors for spaceship mechanisms and solar and thermal power systems for small low orbit satellites”.
These solutions also offer on-line telemetry supervision capabilities for remote real-time data monitoring and transmission.
This two-year SIPRES initiative that will start in the month of October has been funded by ESA within the framework of its TDE technological development programme.
Tekniker has collaborated in the past with ESA and is currently assisting the agency in several projects whose aim consists in studying how the outer space environment affects materials and looking into new ways of producing fuel for space missions.