A new monitoring system for lubricant fluids
The Tekniker technology centre has applied for a patent covering a new system to monitor lubricant fluids and diagnose machine condition to extend service life.
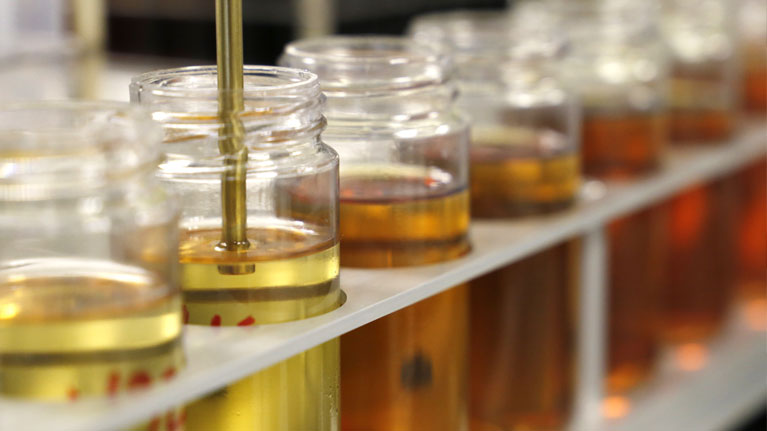
Industrial machines usually use oil to allow their components to operate correctly. In fact, most machine failures are related to lubrication problems. Consequently, lubrication is crucial as failures resulting from a faulty lubrication could increase costs unnecessarily and reduce machine service life.
To achieve optimum machine performance, lubricant fluids must maintain a certain composition and avoid fouling. Consequently, lubricant oil must be constantly monitored as this provides important information on the condition of a machine.
It is in this context that the Tekniker technology centre, a member of the Basque Research and Technology Alliance (BRTA), has filed an application for a new system that allows lubricant fluids to be monitored by a magnetic sensor that checks viscosity. Likewise, this new fluid monitoring system can be used in a number of sectors such as energy (wind turbines), aeronautics, machine tools or maritime operations.
This new fluid inspection system, whose patent application has been filed by Tekniker, is the outcome of the thesis written by the researcher Iñaki Bravo from the Smart Information Systems Unit at the technology centre where efforts are currently focused on developing a new magnetic sensor to monitor viscosity, i.e., liquid flow resistance.
Counting metallic and non-metallic particles in lubricant fluids
Viscosity is a property associated with the film that protects components when directly in contact with each other. When viscosity is too high, oil cannot reach those locations where it is needed and therefore does not perform properly. When viscosity is too low, on the other hand, contact pressure drives the oil out and performance is worsened.
In this regard, the magnetic capabilities this system offers provide an interesting option in terms of sensors used to count particles and viscosity monitoring to check the condition of a lubricant and count how many metallic particles it contains.
By incorporating this viscosity sensor and modifying it according to the above mentioned patent, it is possible to differentiate between metallic particles (i.e., those produced by contacts or other kinds of malfunctions) and non-metallic particles (i.e., those resulting from external pollution).
As explained by Iñaki Bravo, “thanks to this new system, both metallic and non-metallic particles can be counted; as machine diagnostics will also be improved, it means that service live will be extended and that maintenance costs can be potentially reduced”.