Advanced bearings to enhance transport efficiency
IK4-TEKNIKER seeks to develop advanced bearings via the combined use of nanomaterials, surface treatments and new high-performance lubricants.
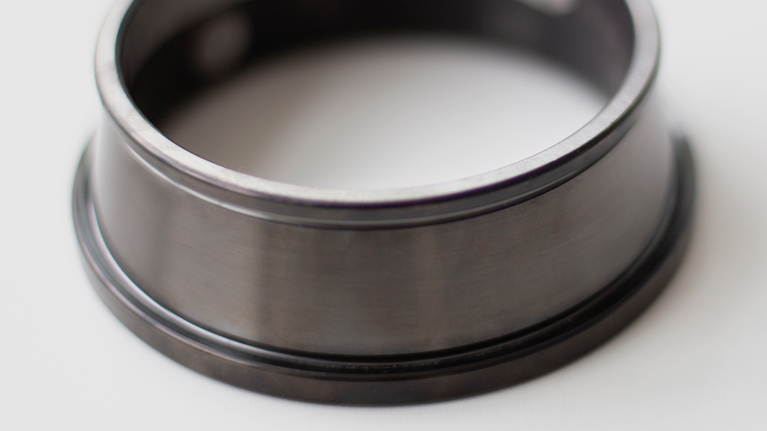
The heavy vehicle manufacturing sector is addressing the challenge of achieving transport that is more efficient and less pollutant, a scenario in which recommendations are focused on developing advanced materials and components.
In this regard, IK4-TEKNIKER is involved in an initiative that seeks to improve the different elements that form part of bearings fitted on vehicles operating under extreme temperature and load conditions by enhancing their performance and extending their service life.
One of the project´s goals consists in developing plastic materials to manufacture bearing "cages" with better tribological properties and in achieving greater compatibility between thermoplastic matrices and the additives selected. (the cage, in fact, keeps rolling elements separated and guided inside the bearing).
Another goal is to develop new coatings that can achieve a minimum improvement of 15% in terms of bearing friction and wear behaviour whilst simultaneously enhancing performance.
Experts will be working to develop new advanced lubricants to increase bearing pressure and speed limits by 20%.
Within the framework of the initiative, solutions shall be validated for bearing materials and elements and fully functional prototypes will be developed. Moreover, pre-industrialisation patterns will be established to manufacture new bearings that can operate under extreme conditions.
Advanced technologies
New low-friction nanoadditive polymeric materials shall be developed to achieve the above mentioned goals for the serial production of new and better performing cages.
New surface treatments will be applied to bearing raceway surfaces to reduce friction and wear and temperature increased resulting from physical contact.
Another area covered by this initiative is related to adapting new lubricants to extreme operating conditions for bearings and to increasing limits in terms of speed and pressure.
Specialisation in surface engineering
IK4-TEKNIKER, specialised in surface engineering, studies tribological designs and performs material and surface engineering to deliver real operating conditions with a suitable interface or lubrication (for example, extreme and controlled environments) with minimal energy expenditure, noise and environmental impacts during the life cycle of a bearing.
Within this context, the technology centre will carry out an exhaustive characterisation of high performance lubricants developed by Brugarolas, a company involved in this initiative.
The centre will also develop advanced coatings by means of the PVD (Physical Vapour Deposition) technology to reduce friction and improve the lubrication of moving components to improve performance and durability, especially under extreme conditions.
PVD processes evaporate a solid in the form of atoms or molecules that are vacuum-conveyed to gradually condensate on the surface of a substrate until a thin layer of specific properties is formed.
The technology centre will also develop protocols for tribological testing to screen the best options (polymeric materials, lubricants and PVD coatings) and also perform simulations under conditions similar to what is found in real environments.
IK4-TEKNIKER, moreover, will characterise the tribological features of new developments in relation to reference values by following the tribological simulation trials that have been developed for this purpose. In this manner, it will be possible to demonstrate the degree of technical performance of the new solutions.
Market impact
The end results will make it possible to discover an innovative solution that is currently not available in the market. The combination of nanoadditive polymeric materials to be included in bearing cages and PVD coatings incorporating a high performance lubricant will give rise to a product that will operate much better.
Based on improvements in terms of bearing lubrication and tribology, the aim is to reduce friction between rolling components to reduce losses and increase overall efficiency.
Moreover, improving bearing performance (pressure and speed conditions) and duration will substantially reduce size and the consumption of spare parts. Consequently, with less raw materials there will be less waste and we will be dealing with an element that is more environmentally friendly.
In addition to Brugarolas and IK4-TEKNIKER, the companies AITTIP and FERSA also participate in the project.