Advanced solutions for dry electroeorsion processes
The IK4-TEKNIKER technology centre has developed a technologically advanced device that facilitates the electroerosion process and does not require dielectric fluids.
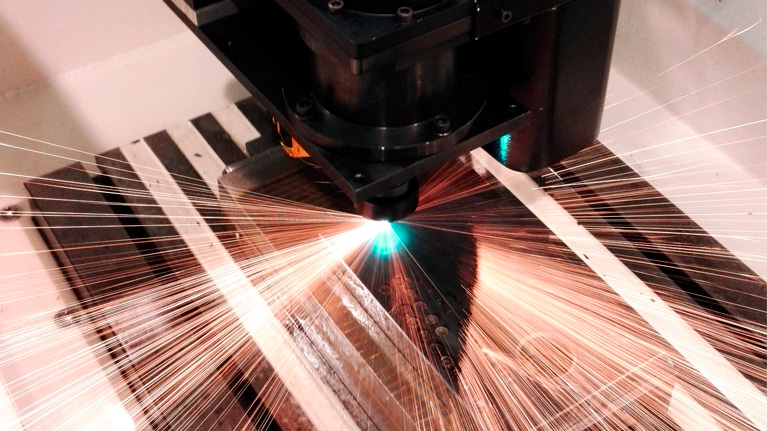
Dielectric fluids must be used during electroerosion machining (EDM) to guarantee the effectiveness and cleanliness of the process. This method, however, generates more waste and higher financial costs.
In order to further progress in the development of processes that do not use fluids, the IK4-TEKNIKER Basque technology centre has been involved in the ELECO project, an initiative that has made it possible to manufacture a device installed on electroerosion machines that allows dry milling operations to be performed.
The solution developed can machine large parts, moulds and dies as well components present in high added value sectors such aeronautics or power generation.
Experts at the technology centre and partners of the consortium, specifically the Basque manufacturer ONA, have developed an independent and dismountable milling head that can can be used on different pieces of equipment fitted with standard electrode holders.
This device, that runs on gas (air) and has an external intake so it can fed from the machine itself or from a cylinder, eliminates the need to use dielectric fluids in electroerosion processes.
“The main goals of the ELECO project have consisted in developing a new machining concept based on clean electroerosion, in opening up new fields allowing electroerosion to be applied to large parts that cannot be processed on the machines currently available and, finally, in furthering the technological development and exploitation of the EDM milling process in gas”, says Manu Goiogana, the person in charge of this initiative at the technology centre.
More specifically, the initiative has made it possible to develop the head in full, from the definition stage up to the requirements, to validate the device on the EDM machine and cover all stages connected to design, manufacture, assembly and checking.
An analysis has been performed to evaluate the behaviour of the EDM process in gas relative to different process parameters such as discharge voltage, intensity, time, diameter, geometry, electrode materials, head rotation speed and the type of dielectric gas used.
“One of the main advantages of the device developed under this project is a reduction in EDM process costs because dielectric fluids have been eliminated. Costs have also been cut back because there is less waste and tooling wear”, says the expert.
As tanks containing dielectric fluid have been removed, it will no longer be necessary to submerge parts meaning that constraints no longer apply in terms of size of parts to be electroeroded. Another benefit is that, thanks to a different layout, floor space can be saved by component manufacturers that decide to go ahead with this technology.
“For manufacturers of electroerosion machines like ONA, these developments will make it easier to create a portable EDM machine concept, an option that has not yet been fully explored. They will also reinforce the profile of these companies as global suppliers of EDM solutions focused on high value”, surmises Goiogana.
Should the Basque manufacturer ONA go ahead and market the head, its degree of coupling to standard electrode holders (EROWA or HIRSCHMANN) would allow component developers to acquire an EDM machine and use this technology on a regular basis.