Artificial intelligence, the best ally for robotics in the field of industrial handling
The Tekniker technology centre has designed algorithms that allow robots to identify grasping points on previously unknown objects to make industrial handling procedures more flexible.
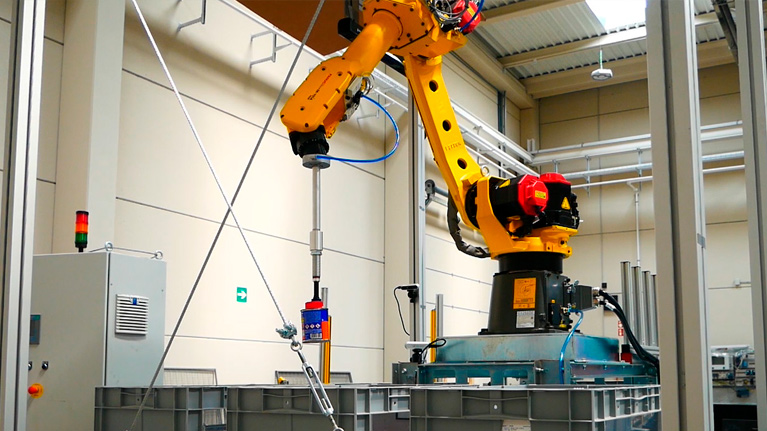
Operations commonly known as pick (using robots to pick up products) and place are basic tasks in most robotic applications in the industrial (machine feeding, assembly or palletising/depalletising) and service sectors (agriculture or households). Consequently, in certain structured environments (within boundaries and without variations) where certain types of parts have to be handled, these automatic processes are thoroughly consolidated.
This, however, is not the case when it becomes necessary to handle parts with a high degree of variability or in less structured environments (without boundaries and with variations). Commercial bin picking solutions cannot be used for applications of this kind as it is unfeasible to configure thousands of references to be processed.
It is in this context that the Tekniker technology centre, a member of the Basque Research and Technology Alliance, has developed new artificial vision algorithms that allow industrial robotics applications to identify grasping points on previously unknown objects sitting inside boxes.
Ander Ansuategi, a Tekniker researcher, explains the “the system we have developed, based on Deep Learning techniques, enables you to directly predict grasping points on objects without having to identify them first. This offers a flexible solution that is capable of handling a large variety of objects”.
Tekniker has also coordinated the technical aspects of the project and has worked on the monitoring system located inside the work area where technical staff and robots share the available space.
The Tekniker researcher also adds that “the aim is to advance in the field of robotic strategies associated with artificial intelligence, handling and flexible grasping, operational precision and reliability to meet the challenges resulting from handling complex products characterised by short production cycles in the logistics sector”.
Software integration
Throughout the initiative, two pilot cases were carried out to see to what extent the artificial vision system developed by Tekniker is actually effective.
On the one hand, the software developed has been installed on an automated order preparation/return unit supplied by ULMA Handling Systems, the project coordinator; and, on the other, the system was put to the test in the area of order preparation procedures involving parts in the TOFAS distributor network. TOFAS is a car manufacturer and a member of the FIAT group.
Thanks to the results obtained in this project it has been possible to transfer advanced artificial vision technologies to the industry at large by setting up automation and robotics solutions to deal with, among other things, unitary orders or machine feeding. Tekniker researchers are currently working on how to include this software in the bin picking solution developed internally.
The PICK-PLACE initiative (Flexible, safe and dependable robotic part handling in industrial environments) has ended in 2021. It is a project that has been funded by the UE programme Horizon 2020 that focuses on developing technologies in the field of handling and grasping procedures in which complex products are involved.
In addition to Tekniker, other partners such as ULMA Handling Systems, CNR-STIIMA, Fraunhofer IFF, Mondragon Assembly and the Turkish car manufacturer TOFAS have also been involved in this initiative.
This Project has received funding from the European Union’s Horizon 2020 research and Innovation Programme under grant agreement No. 780488.