Automating and digitising production processes for a more integrative industry
The Tekniker technology centre is currently involved in the European Masterly project focused on a case study to eventually be commissioned on Aernnova’s production lines
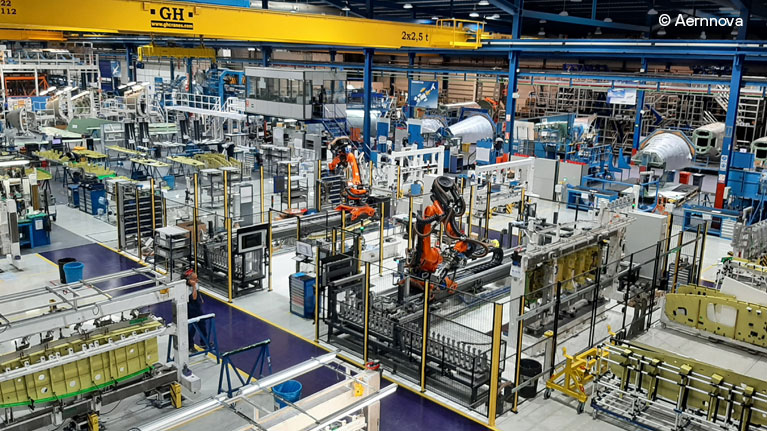
The transition towards a 4.0 manufacturing industry assisted by the automation and digitisation of production processes that allows us to address challenges associated with sustainability, efficiency and profitability is something that not all companies find easy to do. Consequently, this has repercussions with regard to the extent to which companies are competitive in a market that is becoming increasingly global.
It is in this context that the Tekniker technology centre, a member of the Basque Research and Technology Alliance (BRTA), has been involved in the European Masterly project since 2023. Its main goal is focused on furthering technological progress for SMEs so they can achieve a high degree of integration of technological and digital solutions.
In order to reach this goal, a wide range of user-friendly, resilient and smart robotic systems will be developed to enhance efficiency and innovation in industrial processes.
More specifically, Tekniker is providing technological solutions for the case study to be carried out on Aernnova’s production lines to deliver cutting-edge aeronautical structures.
Throughout the initiative, the technology centre will be responsible for integrating automated assistance as well as for the skin handling and loading processes required for the central wing box on the Airbus A220. The organisation will also install a number of sensors (force, dimensional) to monitor the assemblage process carried out on the central wing box.
Automation, monitoring and adaptation
Compared to other existing robotic solutions, this demonstrator (also developed by the Technical University of Kiev, the German RWTH institute, the Greek company CASP and the Italian IIT institute) will be capable of handling a wide range of parts and materials of different sizes and shapes to develop flexible and resilient production lines.
Modular grippers with smart cranes and technologies featuring artificial intelligence (AI) will be used to improve perception and control capabilities.
Simultaneously, and to speed up and perform assembly operations on aircraft structures more efficiently, all processes shall be carried out in a semi-automated environment equipped with additional sensors to continuously monitor production, guarantee the quality of parts and offer workers critical information as an aid for decision making to prevent errors or defects.
One of the key features of this innovation is that it allows operations to be performed collaboratively and with a higher degree of autonomy. This facilitates labour inclusion in the sector as it offers tools and systems specifically adapted to meet the needs of the work environment and of each individual worker.
It is expected, therefore, that operator safety and comfort on the production line will improve. Manufacturing processes, moreover, will be more accurate, efficient and make production more competitive.
Apart from the use case related to the aeronautical sector, the Masterly project covers another two demonstrators associated with, on the one hand, assembly operations for electrical cabinets at Kleeman’s facilities (an industrial manufacturer) where force control solutions used to assemble a number of elements will be developed and, on the other, the incorporation of automated logistics at an order-processing warehouse operated by Decathlon to implement more flexible strategies.
With a total of 16 European partners involved, this initiative that will come to an end in 2026 has received funding from the EU Horizon Europe programme and is being coordinated by the Laboratory for Manufacturing Systems & Automation (LMS) in Greece.
This project has received funding from the European Union’s Horizon Europe programme under Grant Agreement N. 101091800