A technological boost for the circular economy in the aeronautical industry
Tekniker has designed an innovative prototype that will allow aeronautical manufacturers to recycle and recover uncured scrap for use in other sectors to achieve savings and reduce environmental impacts.
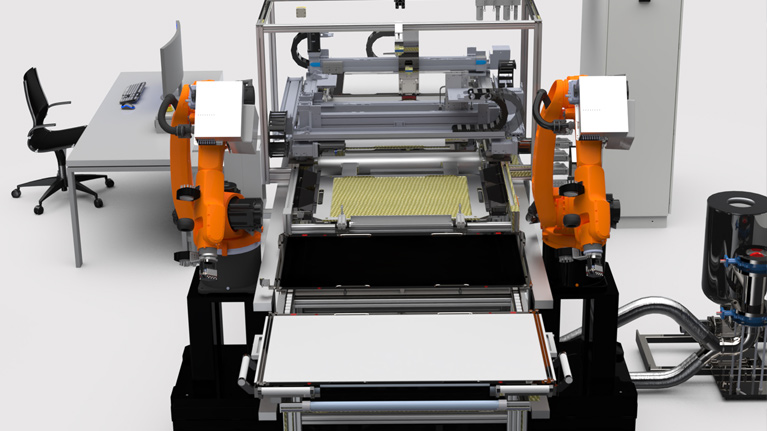
It has been estimated that production in the aeronautical industry in the EU generates approximately 10 tons of uncured carbon fibre scrap containing pre-impregnated resins (prepeg). This type of waste is produced during the manufacture of composite materials and is associated with processing costs ranging between 3 and 12 euros per kilo.
In order to address this reality, Tekniker has designed an innovative equipment that will allow aeronautical manufacturers to recycle and recover uncured scrap on-site to achieve savings and reduce environmental impacts.
The design of the prototype, developed within the framework of the European Recycomp project has already been provided to the Topic Manager, Leonardo Aircraft, and is expected to be ready by February 2023 for the fine-tuning and to run all the tests required to fully validate operations.
Oscar Gonzalo, the person in charge of the aeronautical sector at Tekniker, states that “we have designed a machine that is capable of performing the processes required to reutilise uncured scrap automatically and efficiently, maintaining material properties and quality levels so the resulting products can be used to make new non-critical components, such as cabin elements, or for other sectors”.
Artificial vision and robotic systems
In order to develop this solution, the Tekniker team has brought together several processes and technologies to allow the system to perform recycling automatically.
Artificial vision equipment has been used to identify unsured scrap and the orientation of carbon fibres. The information obtained is processed by software that has also been developed by Tekniker that helps the equipment make regular cuts according to predefined fibre direction patterns by means of a cutting head fitted on the machine.
Robotic systems are used at a later stage to manipulate cuttings in a regular manner and generate orderly mosaics containing the cuttings which produces a sheet made up of surplus material with controlled mechanical properties.
The project also includes the production of test specimens and samples to run tests to evaluate the mechanical properties of the recycled materials for comparisons with the properties of the original materials. All this with a view to reuse and thus obtain environmental benefits through a circular economy model.
It is expected that the entire system will up and running at Tekniker’s facilities by February 2023 to carry out the fine-tuning required for the recycling process. It has been estimated, moreover, that the equipment will be installed in Italy by the month of March to allow the Topic Manager to produce an initial batch of recycled materials and run tests for material characterisation.
This European RECYCOMP will close in August 2023. It has been funded by the EU Clean Sky 2 programme whose ultimate goal is to find solutions to improve mobility within the EU and meet the goal of reducing CO2 emissions by 75%, NOx by 90% and noise by 65%.
RECYCOMP project has received funding from the Clean Sky 2 Joint Undertaking under the European Union’s Horizon 2020 research and innovation programme under grant agreement No 886967.