Electromagnetic actuators and machines
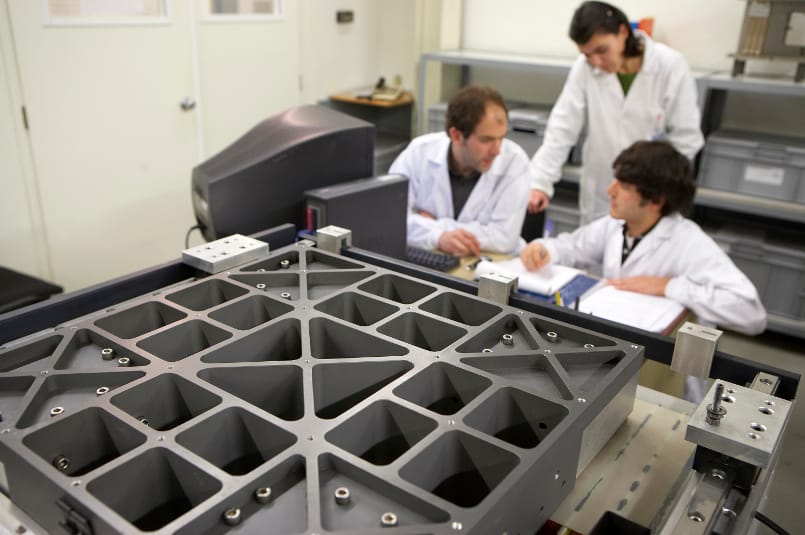
TEKNIKER has wide experience in the field of electromagnetic actuators at their different stages of development; from their conception and design, through their manufacture, and to the trials stage. This theoretical knowledge of the different areas involved (electromagnetism, mechanics and control) and the practical experience in real applications is transferable to new applications and challenges that may arise.
The magnetic bearings were initially developed for milling applications and subsequently the technology began to be applied to kinetic energy storage (inertia wheels), for short-period (about 20 s) energy storage applications. The most recent developments have been applied in choppers for neutron spallation source installations.
Other examples of electromagnetic actuators in which work has been undertaken are:
- XY positioning table activated by magnetic linear actuators.
- Electromagnetic design of a permanent magnet linear generator for wave-sourced energy
- Dimensioning of a system for reducing forces on lift (elevator) guiderails.
Specialisation is currently focused on the design of rotary electric motors for the automobile sector, other traction applications (torque-motor) and the industrial sector (machine-tools and multi-phase machines).
The main areas for technical development are:
- Modelling: mechanical modelling of a system with magnetic bearings, electromechanical models for electric machines (asynchronous machines, machines with magnets, switched reluctance machines and multi-phase machines).
- Calculations: electromagnetic, mechanical, thermal. Analytical and finite elements.
- Design: electromagnetic and mechanical. Optimisation of geometry based on electromagnetic and thermal criteria.
- Rotor dynamics: calculation of natural frequencies, permanent regime, and model generation based on state-spaces for simulation in time.
- Control: implementation of real-time control with sample frequencies of up to 20kHz, SISO and MIMO algorithms, vector control of machines, rotary electric ones, modulation (FPGA), buffer algorithms, etc.
- Assembly process: calculation and design of rotor connections with interference. Experience in the design and undertaking of dismountable connections through hydraulic systems for uniting elements that cannot be subjected to heat: for example rotors of magnet motors and inertia wheels made from composite material.
- Vacuum: kinetic energy storage applications require high vacuum levels in order to minimise the energy losses in the rotor of an inertia wheel. TEKNIKER has the knowhow required to develop these types of systems: mechanical design, knowledge of the behaviour of the insulation systems depending on the vacuum level, and so on. High-current (400 A) vacuum connectors have been developed as a result. TEKNIKER is currently at the stage of developing of a drag pump that will enable increasing the vacuum level in the interior of the inertia wheels, thus taking advantage of the vacuum already in the rotor spinning inside the wheel.