Eliminating lead from large-sized engines
The IK4-TEKNIKER R&D centre is working on the BeLeadFree project, which is aiming to eliminate lead from the bearings built into the engines of heavy diesel vehicles used in road transport, electrical power generation and maritime transport.
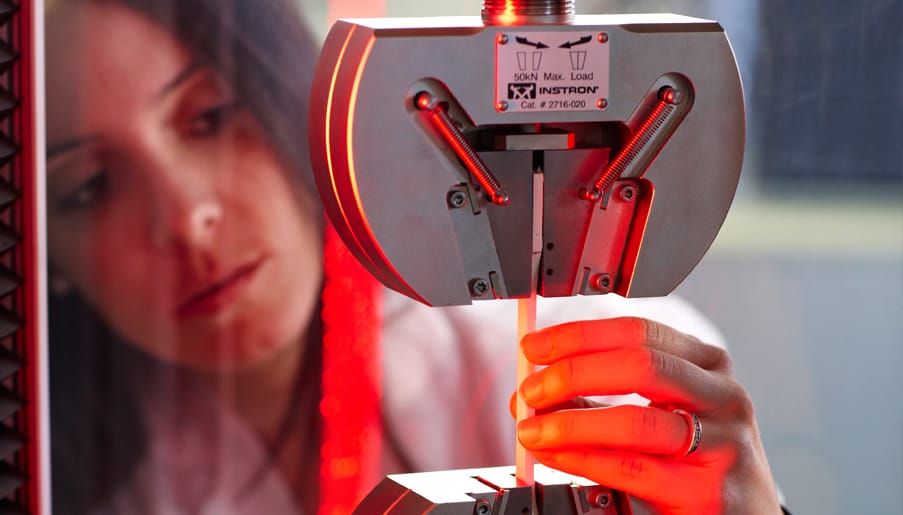
With the aim of continuing to drive forward the structuring of more efficient and less polluting industry, the Basque R&D centre IK4-TEKNIKER is participating in a European project focussing on the development of a new range of lead-free bearings for large-sized, high-performance engines.
The initiative, known as BeLeadFree, is being coordinated by the British manufacturer of automobile bearings Daido Metal and has the participation of the Belgian company Elsyca and the University of Coventry (United Kingdom).
The project, which kicked off recently and is set to run for two years, has funding of nearly 3 million euros approved within the programme designed to encourage innovation within the European Commission’s Horizon 2020 programme.
The project is seeking to develop multilayer engine bearings that are highly friction- and wear-resistant and manufactured using alloys free of lead, the material most widely used today to manufacture these components.
Bearings are parts used by engines to minimize the wear of the elements that perform rotatory movements. Until now, lead has been used to manufacture these parts but its high polluting level and toxicity make it necessary to seek alternative alloys free of this element.
All the products being developed in this project are geared towards medium heavy-duty and heavy-duty diesel engines used in heavy commercial vehicles, ranging from large two-stroke or four-stroke medium-speed engines used in seagoing vessels right up to submarines or generating sets.
IK4-TEKNIKER’s Tribology unit will be responsible for carrying out the laboratory simulation of the wear mechanism of the new bearings developed and of the current ones by means of short tests and in conditions of extreme precision; all this is designed to predict the useful service life of these bearings.
IK4-TEKNIKER will be carrying out the advanced characterisation of the materials of the new lead-free bearings, the composition analysis, the microstructure, the supervision of the surface characteristics such as morphology, hardness, roughness or the contact angle as well as the study of residual stresses and mechanical and tribological properties.
The specialists will be testing the various lead-free alternatives, selecting the ones that offer better mechanical and tribological performance, less friction, wear and greater resistance to extreme pressure, and will also be verifying that these new alloys are environmentally friendly.
To achieve this second objective, the wear particles produced in the tribological test and in the engine tests will be gathered and they will be subjected to ecotoxicity tests in order to confirm that they are not toxic.
“It is essential to guarantee that the new alloys generate low friction so that fuel consumption can be cut, that they have a duration similar to the lead ones currently in use, and that they withstand high pressures and speeds to guarantee that the industry can safely replace them, but also that they are less toxic and contaminating and more environmentally friendly than the solutions used until now,” stressed the head of IK4-TEKNIKER’s Tribology Unit Amaya Igartua.
The bearings developed within the framework of this project will be useful in industrial sectors such as electrical power generation, engines for seagoing vessels and heavy vehicles in the automotive sector.
This project has received funding from the European Union’s Horizon 2020 research and innovation programme under grant agreement nº 691503.