Fault prediction based on test bench simulations
IK4-TEKNIKER is implementing integrated procedures that include the development of tests performed on test benches, virtual simulations, real operation monitoring and the application of advanced analytical techniques to diagnose and predict equipment and component status for maintenance management optimisation.
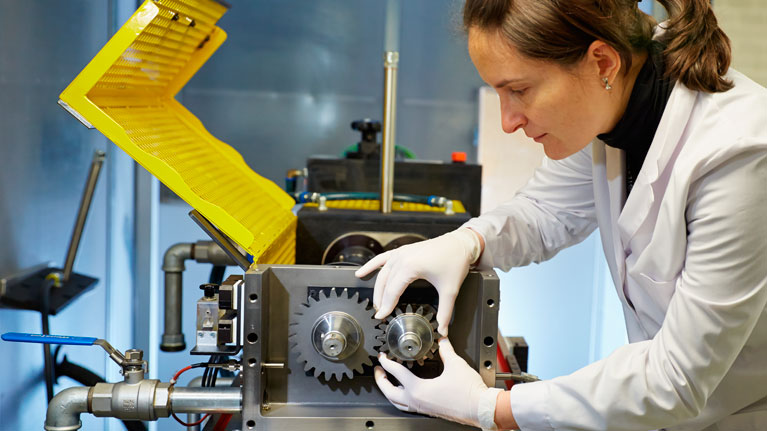
Continuous breakthroughs reported in terms of Industry 4.0 have resulted in smart and connected machines as well as equipment and components that can produce data related to their maintenance requirements.
This information provides end customers with a fundamental added value that increases the efficiency of their processes and gives them a competitive edge. It is also provides a new business model for manufacturers that is based on delivering maintenance services for their equipment (servitisation) throughout the entire life cycle.
From data to knowledge: procedure and approach
Major breakthroughs in terms of data modelling and analysis techniques offer significant opportunities as regards the possibility of developing predictive models to trigger alarms related to fault conditions.
Techniques such Machine Learning and Deep Learning help to select and understand which indicators are relevant to identify anomalies and predict how they will evolve. Predicting faults, however is not easy.
Simulation techniques also play an outstanding role as regards enriching predictive models. Virtual simulation allows you to characterise the digital model (digital twin) of a piece of equipment and simulations performed on test benches can deliver behaviour characterisations by testing equipment under extreme conditions.
Test benches to simulate equipment and component behaviour
IK4-TEKNIKER has extensive experience as regards developing test configurations and procedures used to validate critical components.
Specifically, the organisation´s experience is based on designing components, equipment and machines; on learning more about component failure and degradation mechanisms; on the development of sensors and signal acquisition systems; on developing customised test benches according to customer needs; on designing specific testing protocols; and on processing signals and identifying indicators.
The simulation of components on test benches specifically adapted to each case study supplies the knowledge required to understand how equipment and components behave when in use, both under real operating conditions and extreme or accelerated conditions. IK4-TEKNIKER has a complete tribology laboratory equipped with approximately 26 tribometers and 7 test benches. Hereunder are listed several of said units:
- The FZG gear test bench used to analyse wear, surface fatigue, vibrations, transmission errors and power losses. Tests can be performed subject to standards or according to adapted procedures. Lubricant and oil analyses.
- The TESSA test bench to analyse sealing systems by assessing friction, wear, leaks, efficiency, etc., and simulating real operating conditions and configurations.
- Test benches for bearings to analyse lubricants, grease, surface wear phenomena, vibrations, WEC, component failures, etc. Tests are performed according to standards (DIN 51819) or proprietary testing procedures.
- The GPS test bench to simulate and diagnose failures involving gearboxes.
Ultimately, knowledge related to how components behave when in use allows business models to be developed that are based on servitisation and focused on providing advanced maintenance services for equipment.