High productivity laser micro-drilling for the aeronautical sector
IK4-TEKNIKER is developing a machine based on laser technology to manufacture large microperforated panels for stabilisers on commercial aircraft.
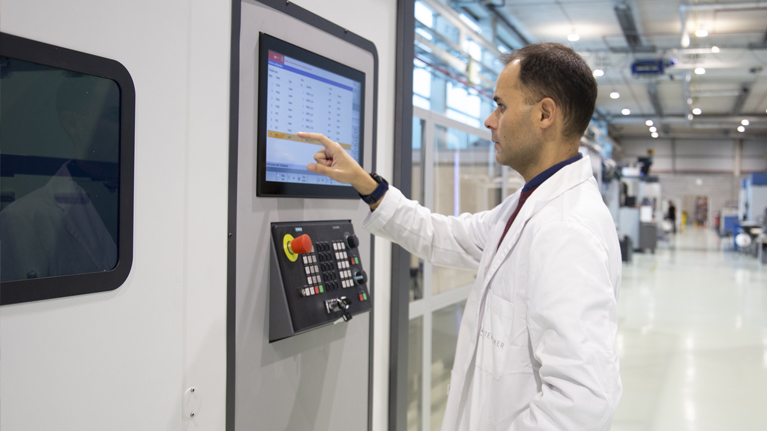
Air transport has grown significantly in recent years and further growth has been predicted as forecasts show that current traffic figures will double in a matter of only two decades. Consequently, this increase will have a significant environmental impact due to increased greenhouse gas and more pollution.
Structural weight, aerodynamics and energy efficiency are the key research areas in an aeronautical sector that has done its utmost for many years to discover techniques that can minimise aircraft air resistance to reduce fuel consumption and pollution.
One of the most promising techniques is called HLFC or Hybrid Laminar Flow Control for wing structures and tail stabilisers. Thanks to this technology, air can be sucked through tiny holes to lessen resistance.
Solutions of this kind could save up to 10% of fuel consumption and achieve a significant reduction of CO2 and other contaminating agents such as NOx.
Industrial production processes, however, of microperforated metal panels for leading edges of tail stabilisers and wings represents one of the biggest challenges as regards developing and implementing the HLFC technique specifically for commercial aircraft.
It is within this context that IK4-TEKNIKER together with the German technology centre Bremer Institut Fur Angewandte Strahltechnik (BIAS) and Aernnova have jointly designed, developed and assembled a unique prototype of a high productivity laser drilling machine to manufacture HLFC panels to be installed on the leading edges of aircraft tail wings in the future.
The machine has been designed to process titanium panels measuring up to 5000 x 2000 x 0.8 mm at speeds in excess of 300 drillings. This unit is to be validated and tested in an industrial environment.
It also features a number of monitoring and control systems to ensure optimum panel quality and each drilling can be checked individually.
A focus on laser technology
When installed on a machine, laser technology allows tapered holes to be drilled with different aspect ratios. The unit can produce inlet and outlet drillings measuring approximately 0.100 mm and 0.050 mm in diameter, respectively, and maintain a dispersion of less than 0.005 mm.
Other process can also be performed with the machine such as cutting, marking, etc., to improve end quality and facilitate subsequent component manufacturing processes.
In short, the machine that is being developed will be able to reduce commercialisation lead times for HLFC structures and also bring about a fast large-scale implementation of this new technology in the aeronautical sector.
IK4-TEKNIKER will present the design of this machine at the 22nd edition of the Conference on Advanced Manufacturing and Machine Tools that starts today at the Gipuzkoa Science and Technology Park and closes on Friday.
Specifically, the presentation itself will be given on day two of the conference, October 24th, during the scientific-technical section dealing with machine tools and their components. This session will also be chaired by Javier Arzamendi, deputy director for technology at IK4-TEKNIKER.
In addition to presenting this new design, IK4-TEKNIKER will also have an outstanding presence in other scientific-technical sessions of the conference and give presentations on additive manufacturing and precision systems installed on machines.
This project has received funding from the Clean Sky 2 Joint Undertaking under European Union´s Horizon 2020 research and innovation programme under grant agreement n° 755620.