Industrial maintenance: Data analysis
Condition-based maintenance allows faults to be detected before they occur, and in that way for maintenance to be carried out at the right moment and in a planned way. In this respect, IK4-TEKNIKER is offering support in everything to do with data and information analysis.
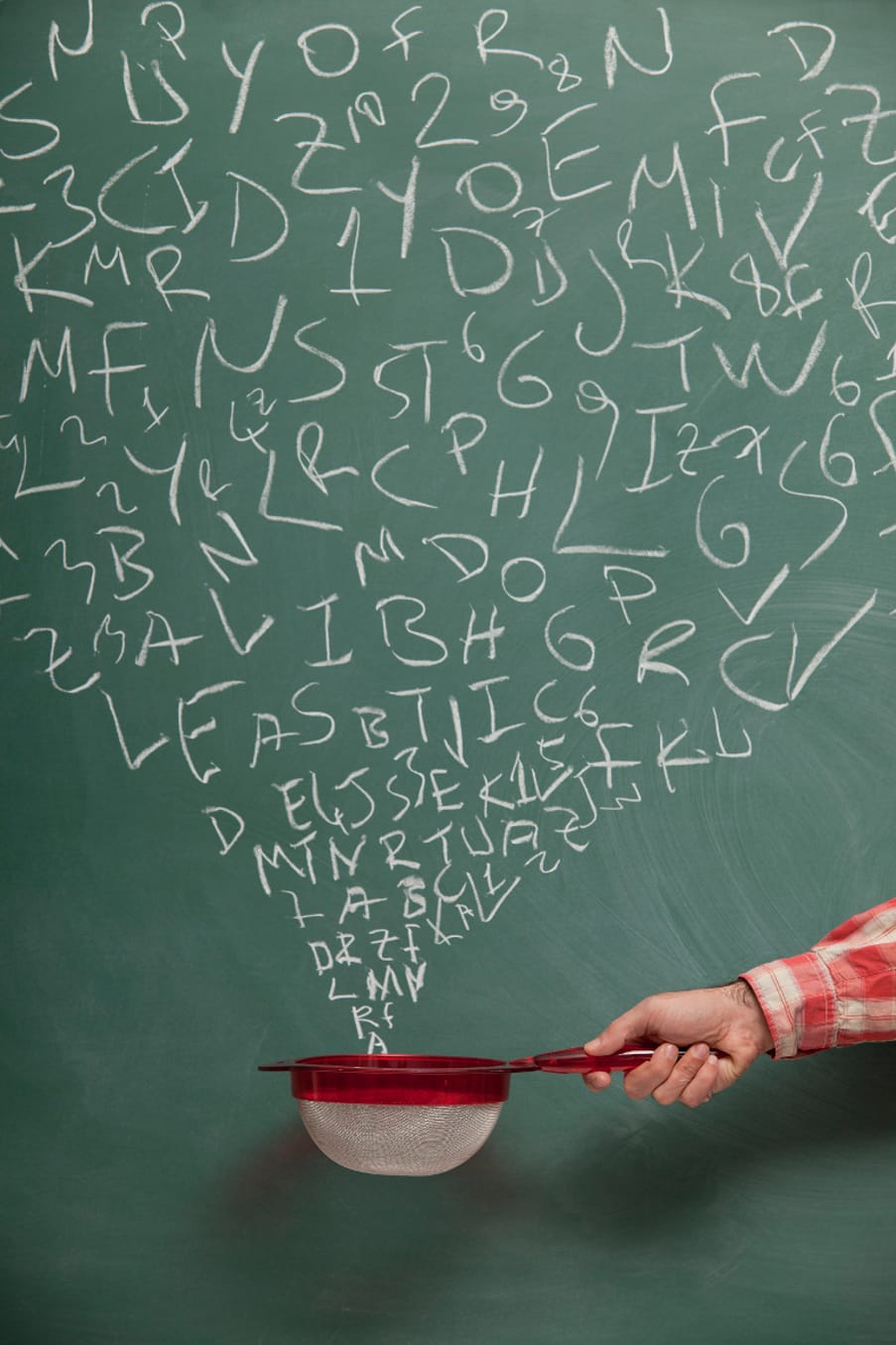
The new needs in productivity, flexibility and dependability are forcing companies to seek strategies that will improve their processes and services in order to maximise their results and minimise costs. That is why maintenance is evolving to become a key component for many business models. Maintenance accounts for 9.4% of GDP, according to a recent study by the Spanish Maintenance Association (AEM).
There are various strategies that can be used when it comes to conducting maintenance in industry. It is very important to know which the most appropriate one is in each case, since the necessary resources have to be optimised.
Corrective maintenance (waiting until something fails) is seldom an option in all systems, either because of the expense that may be incurred by a downtime or else because of the costly nature of the repair. The average cost of downtime in an automotive plant is reckoned to be between 1 and 3 million euros per hour.
So the most widespread option is to carry out preventive maintenance in a systematic way, make adjustments or replace certain components of a system, the oil, for example, in a systematic way; but this may be costly and often ineffective.
There are studies indicating that 30% of the preventive actions could be avoided and that the other 30% could harm the equipment, as carrying out maintenance tasks could affect the useful service life of a component.
The type of maintenance that is gaining ground is condition-based maintenance, thanks to the advance in technologies. The aim is to spot faults before they happen so as to be able to remedy them, and thus carry out the maintenance at the right moment and in a planned way.
Predictive Maintenance
With this view in mind, IK4-TEKNIKER´s technological offer for maintenance and dependability is focussing on offering companies support to enable them to increase the availability and dependability of their assets.
IK4-TEKNIKER offers support in everything to do with data and information analysis. Ranging from help in identifying improvements in maintenance processes to the use of technologies that facilitate operation decision-making. There is even a methodology available to understand what the best economic option is with respect to the strategies to adopt.
Bearing in mind that predictive maintenance is one of the strategies to be encouraged, the data that can be extracted from the use, performance and condition by means of data mining techniques are studied in order to spot abnormalities with respect to normal conditions and which can help in the diagnosis and prognosis of faults.
Simulation for health monitoring
Another of the capacities that can allow knowledge and information to be extracted from the data is through test benches and existing modelling systems; this way, it is possible to simulate different breakdown situations in controlled environments.
By using indirect measurements the necessary knowledge is gathered for the detection, diagnosis and prognosis of faults and which can then be integrated in an ideal way into health monitoring systems. This is very useful in new products or in products in which the field measurements may not be the most ideal ones for the tests (aeronautical systems).
All this information extracted plus knowledge of ICTs makes it possible to monitor the various assets in a controlled way by means of software systems based on the new concepts of cloud computing and the internet of things. In this area, work is being done on platforms that can allow users to make rapid decisions and analyse the various assets of the company.
Success stories
Some examples of projects in which work has been done or is being done are as follows:
In the aerospace sector and specifically in a project in which IK4-TEKNIKER participated alongside companies like Airbus, EADS, Gamesa, Eurocopter, Air France, Smiths Aerospace and Snecma, the aim was to improve the maintenance strategies being applied in commercial and military aviation where maintenance can end up accounting for up to 20% of an airline’s costs. IK4-TEKNIKER participated as an expert in diagnosis and prognosis technologies in which knowledge relating to dependability techniques plays an important role.
As regards capital goods, an embedded system capable of monitoring and assessing a machine’s state of health has been designed; it uses information about energy obtained from energy and current sensors, etc. and the machine’s accessible data.
In addition, the aim is to use these indicators to manage the improvement of the business, bearing the following three concepts in mind: optimising prediction-based maintenance strategies, managing energy as a production resource, and allowing manufacturers to gather information on the use and dependability of their machinery. IK4-TEKNIKER is leading this project and is working to develop the various algorithms that will enable the health of the machinery to be established.
In wind energy, work is being conducted on new systems of component monitoring and predictive maintenance geared towards managing wind turbines and wind energy parks. IK4-TEKNIKER is working on the development of new hardware and software technologies for modelling and automating supervision and support in decision-making for process systems and asset management. This involves the modelling of systems in which it is necessary to take into consideration physical characteristics, trends and parameters of the condition, data templates and/or the technical knowledge from back data.