Machine tools and maintenance 4.0
IK4-TEKNIKER is developing technologies to provide failure detection and continuous characterisation of equipment condition. The technology centre will showcase developments made in the field of predictive maintenance at the next edition of the Spanish Machine Tool Biennial (BIEMH).
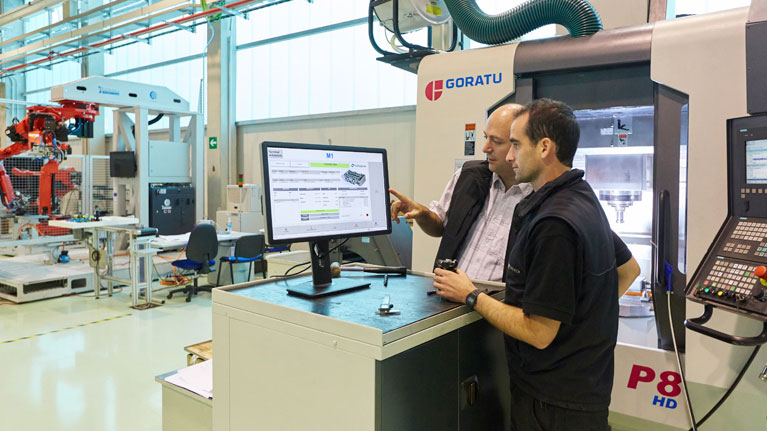
Sectors related industrial manufacturing and machine tools are currently demanding new predictive maintenance systems that are capable of anticipating failures, planning shutdowns, extending equipment availability and reducing costs in terms of servicing, maintenance and operation.
It is therefore crucial to establish an integral approach both for equipment and the operating environment by applying cutting-edge know-how with regard to data collection, analysis and processing.
The IK4-TEKNIKER technology centre has focused on the combined use of information and communication technologies for the purpose of detecting, diagnosing and predicting faulty operations involving mechatronic systems.
It will be during the next edition of the Spanish Machine Tool Biennial (BIEMH) to be held from May 30 to June 4 when the technology centre will make the most of the event in question to showcase the work carried out in the field of predictive maintenance.
The strategy applied to equipment maintenance to date has mostly been based on preventive actions supported by a reactive approach to failures. Systems of this kind, however, have a significant impact on the quality of a process due to increased costs, lower productivity and uncertainties with regard to machine reliability.
Machines, moreover, are equipped with critical components such as headers or linear guideways and this means that cost reductions connected to repairs represent a key goal. Avoiding 75% of the failures involving these components could increase overall machine availability by up to 10%.
In order to significantly reduce the number of breakdowns, IK4-TEKNIKER is using predictive know-how and tools to pinpoint problems and continuously characterise equipment condition. This means that maintenance actions are fully in line with real requirements and that interventions can be planned accordingly without losing sight of production and operating constraints.
IK4-TEKNIKER’s contribution
As Maintenance research efforts in the past focused primarily on processes, it meant that machine condition monitoring for failure detection was neglected. Techniques such as vibration and temperature analyses are currently addressed in the different stages of engineering, testing and assembly.
Predictive maintenance, however, is based on the combined use of technologies to enable the collection, processing and reviewing of data related to the equipment used to draw conclusions, identify anomalies, make diagnoses and predict behaviours.
IK4-TEKNIKER has a solid and long-standing experience as regards developing test benches and modelling systems that simulate a range of error situations in controlled environments. Indirect measuring delivers the knowledge required for the detection, diagnosis and forecasting of any incidents that can be addressed by means of condition monitoring systems. This process is very useful for new products or scenarios in which field measurements are not fully suitable to run tests.
All of this information, together with the support provided by ICTs, provides controlled equipment monitoring by means of software based on Industry 4.0 concepts such as cloud computing or the Internet of Things.
The IK4-TEKNIKER research team assists companies in their development of predictive maintenance systems based on the requirements of the business, its failure modes and machine behaviour patterns. On the one hand, it delivers the embedded system required to locally process information and later communicate with the cloud. On the other, it supplies development techniques for layers of ‘middleware’, business intelligence and ‘machine learning’ when information is being processed and analysed to manage data as efficiently as possible by using the most suitable platforms and infrastructures for each specific case.
Predictive maintenance is a key discipline for the evolution of industry 4.0 based on applying information and communication technologies in manufacturing environments.