Metrology opts for machine tools
Interview with Javier Orive, Quality Control Manager at Zayer
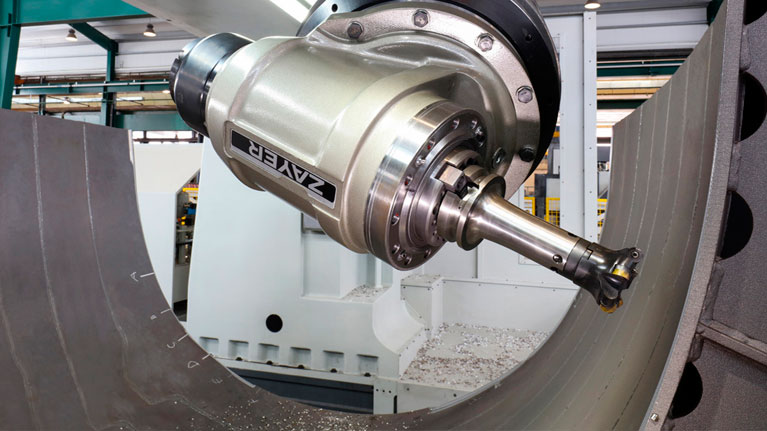
Javier Orive is the Quality Control Manager at Zayer, a company that has been developing milling machines and machining centres since the 1940s. During this interview, Orive shares his views on a number of landmarks connected to how relevant metrology has become nowadays in the machine tool sector.
1.- A growing demand for greater accuracy in manufacturing processes has meant that innovative alternatives had to be found in the field of metrology. This reaches out to several sectors, including machine tools, their verification and commissioning. How is Zayer addressing these new needs?
We are developing automatic running “utilities” at Zayer to check header geometry and adjustments.
Zayer has iCAL, an in-house smart calibration application that delivers full information on the current condition of a machine and performs self-adjustments for the kinematics and geometries of our automatic rotation header by running a sensoring programme.
2.- Zayer was one of the main stakeholders in the INTEFIX consortium featuring 30 companies and technology centres whose goal was focused on upgrading the performance of machining processes by using smart systems. What role does metrology actually play in these processes?
Metrology is indispensable for current manufacturing processes, especially so for those in which it is difficult to control the outcome of the measurement process itself due to the variability of critical parameters or because of a lack of control of the real scene (geometry, toolings, thermal status, drift, etc.).
Integrated dimensional metrology provides manufacturing with the necessary means to get to know and control production processes better.
During the INTEFIX project, this integration has been solved via an interaction between a smart mechanism and the machine tool itself. This mechanism enables us to measure the true geometry of a work piece to accommodate machining programmes to its real shape and dimensions. This is how high accuracy machining can be guaranteed.
3.- Within the framework of the HIPERION project, Zayer’s machines have played the role of test benches to develop a volumetric verification and compensation procedures carried out in cooperation with IK4-TEKNIKER. Could you explain some of the details of this cooperation?
Our view is that the HIPERION project has been a landmark in the cooperation involving both organisations as it has allowed Zayer to acquire theoretical knowledge on the volumetric verification of machines and IK4-TEKNIKER has been able to transfer its developments to a real scenario.
Thanks to the project we were able to look into the origin of a number of deviations that occur at the tip of the machine tool when a machine shifts its entire work volume.
4.- How significant is it for Zayer to be able to cooperate with other stakeholders in this sector?
By cooperating, knowledge can be exchanged. In Zayer’s case, it has allowed us to become involved in the design of structural components. It means we can improve volumetric accuracy without having to make any corrections.
5.- The innovative character of Zayer linked to its eagerness with regard to achieving continuous improvements means that the company is permanently in touch with R&D&I processes. How much weight is attached to metrology in the machine tool sector? What sort of challenges will there be in the future?
Metrology has acquired a significant dimension in terms of heavy duty machines such as those manufactured by Zayer.
Our main aim is to guarantee the accuracy of large pieces when working in non-climatised workshop environments.
To that end, we build machines featuring mathematical algorithms that allow you to take into consideration variations that are inevitable in terms of environmental conditions.