Mobile machine tools: small solutions for big problems
The expert’s view: by Josu Eguia, IK4-TEKNIKER’s Researcher
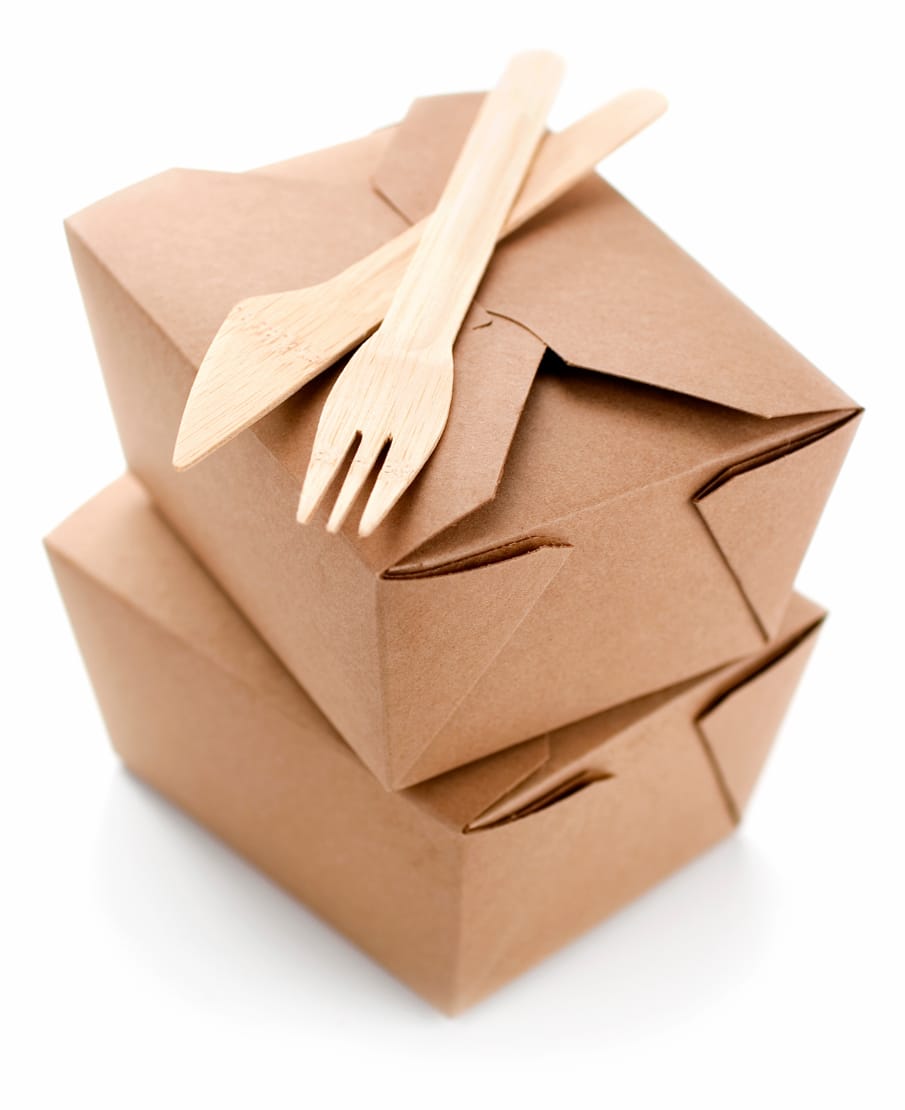
We are immersed in an increasingly globalised economy in which knowledge, equipment and products can travel more freely than at any other moment in history. In recent times, we have been witnessing the trend to relocate industries based on low added-value products and labour-intensive manufacturing processes. So the manufacturing of a large quantity of goods has moved towards places with lower salary costs. However, in the processes and parts of great responsibility this trend is much slower, if not non-existent. The more consolidated economies can take advantage of this niche by specialising in the Advanced Manufacturing of high added-value, knowledge-intensive products.
A particular case of a part or product of this type are very large machined parts, for example, those needed in the driving force sectors like the shipbuilding industry, wind energy, large scientific facilities, etc. These parts combine great responsibility in service and challenging sizes.
During the manufacture, repair and maintenance of these large parts, huge machine tools adapted to the target parts are used. The Basque Country’s machine-tool manufacturers have clearly been specialising in the production of small series of large-sized machines.
However, this approach poses considerable problems of many kinds. Large machines are complex in terms of their design and call for considerable investments during the manufacturing, assembly and commissioning processes. So technically and organisationally they pose a very complex challenge for any company.
What has become apparent in recent years is that on most occasions the geometry to be machined is not very large even though the part itself may be large. That is why the use of large machines is frequently not the best solution and entails considerable costs since their high operating costs have to be added to those of moving the parts from the place where they are used to the workshops. This transport can also be hazardous and slow, leading to prolonged downtimes.
What has been proposed for these cases is a change of model that seeks to end the dogma of “large machines around and for large parts” in favour of new, small-sized machine tools that can be transported to the location of the part in service and which can be freely positioned on the part. Once in place, they can perform the machining work with a quality equivalent to that of the large machines. These small, intelligent machines, which are taken to the part and are free to move around and work on it, are conventionally called mobile machines and are the basis of the fresh approach: “small machines on large parts”.
A path to be covered
IK4-TEKNIKER has developed mobile machine solutions with parallel kinematics and with serial kinematics. Once fitted, these machines can automatically self-calibrate themselves to specify their position and orientation and get down to work on the part. That way, very complex operations have been successfully carried out on large parts like aeronautical turbines, automotive dies, etc.
These mobile machines weigh just a few hundred kilos and can be taken to the application in a small van; that way, the whole process to repair the part is simplified. The solutions are reasonably precise and are competitive with respect to traditional systems in some specific applications. Their structures are optimized to achieve a high rigidity to weight ratio, are uniform in all directions within the working space, have low levels of vibrations and are chatter free. What is more, these machines have been fitted with the most advanced numerical controls without either performance or user experience being adversely affected, thus making them straightforward to use by operatives. So they offer part of the functionality of a conventional machine plus all the freedom, autonomy and mobile capability described.
We at IK4-TEKNIKER are endeavouring to offer and demonstrate comprehensive technological solutions, from the idea, the development of the process and going right up to the creation of the advanced equipment that offers industry a comprehensive solution.
Obviously, there are still technological aspects that remain unresolved in these models of machines; IK4-TEKNIKER is working on them to ensure that these new solutions can succeed in changing manufacturing methods and the type of machine produced and used.
The miniaturization of the machines needs to be improved without either flexibility of use or the capacity to carry out complex operations being lost. Furthermore, these machines need to be provided with greater autonomy and intelligence through the use of information obtained from a whole host of sensors, thus allowing the locating and referencing of them with respect to the part, etc. With the advances anticipated, the machines could redo the part programmes automatically in order to adapt to the situations in which they have to work.
The processes and equipment developed need to go on being tried and tested in an industrial environment so that their long-term behaviour and economic impact on the company can be validated; these are two key indicators if the potential user industry is going to take up this new model of machine.
IK4-TEKNIKER is making significant progress in all these challenges, so in the short term it is going to be offering comprehensive solutions that can be transferred straight to industry.