New corrosion and wear resistant coatings for biomedical uses
The IK4-TEKNIKER R&D centre has developed a range of technologically advanced materials to coat dental, knee and hip prostheses; they are corrosion and wear resistant and increase implant durability.
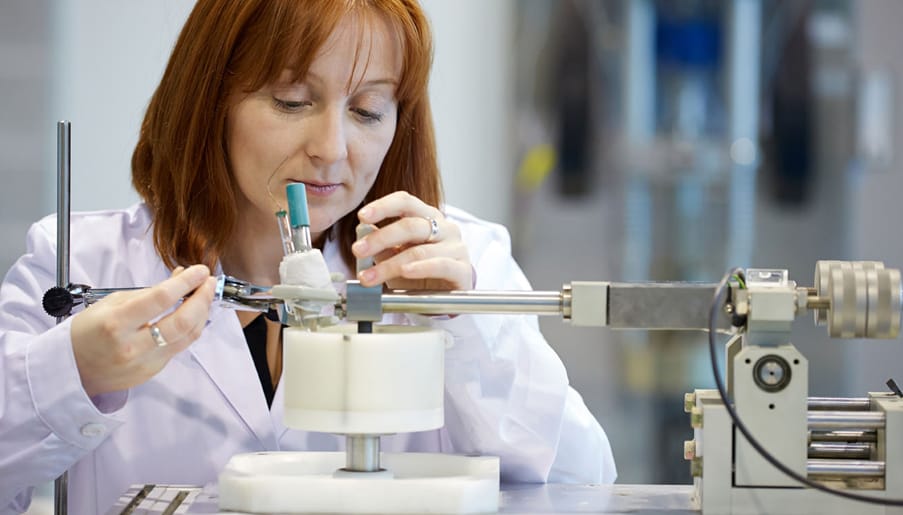
In order to prolong the service life of prostheses for biomedical use, the IK4-TEKNIKER R&D centre has designed technically advanced coatings that resist corrosion and wear. These materials protect knee, hip and dental implants efficiently and in a way that is safe for health.
Tribological causes are the main reason why medical implants fail; in other words, because of the behaviour of materials that are in friction in an environment with very specific characteristics. The prostheses are inserted into a corrosive medium in which they come into contact with biological fluids. Titanium biomedical alloys used in implants of this type have displayed high resistance to corrosion, yet in the sliding and friction functions with other materials titanium sustains significant wear.
This phenomenon may lead to the appearance of wear particles that could cause the early failure of the prosthesis, so obtaining a range of resistant coatings is a key aspect in prolonging the useful service life of the prostheses.
In this context, the R&D centre has developed a biocompatible tantalum nitride (RaN) coating that protects against corrosion and wear and which is deposited by means of PVD (Physical Vapour Deposition) technology.
Tantalum nitride coatings significantly reduce the friction of the tribological system and cut mechanical and chemical wear (due to corrosion) by 98% over the titanium substrate.
What is more, the researchers have also designed DLC (Diamond Like Carbon) coatings that use the same technique, and finally surface treatments based on Plasma Electrolytic Oxidation (PEO).
The R&D centre also carries out accelerated wear and corrosion testing in biological mediums; these tests make it possible to estimate the durability and behaviour of the materials and coatings destined for the manufacture of artificial prostheses or dental implants.
“These technologies give rise to corrosion- and wear-resistant coatings. Right from the start IK4-TEKNIKER has been devoting its attention to the study of this field in which it has a long trajectory,” said the research coordinator Amaya Igartua.
The expert believes that bringing the results to the market will not entail any complexity because PVD technology is involved in 80% of industrial cutting tools.
The materials developed by IK4-TEKNIKER can be applied in the first instance to sectors such as biotechnology, biomedicine and healthcare, although the solutions developed could also be valid for the aerospace and automotive sectors, among others.