New machine tool simulation platforms
The project lies within the framework of the so-called fourth industrial revolution and focuses on applying digitization techniques that are giving rise to a new production model. Results will be validated in the aerospace and automotive business, two of the most strategic economic sectors.
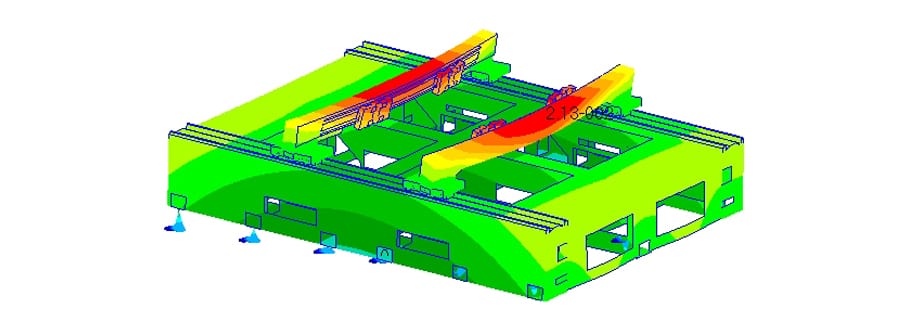
Improvements in energy efficiency, the implementation of predictive maintenance and increased productivity levels are key elements to guarantee European industrial competitiveness. In order to design strategies featuring the above in the manufacturing sector via a technology transfer approach, the Basque technology centre IK4-TEKNIKER is currently coordinating a European project whose aim is to design a simulation platform for machine tools and machining processes.
The initiative lies within the framework of the so-called fourth industrial revolution, or “Industry 4.0”, that applies innovative digitization techniques geared towards developing a new production model supported by the incorporation of advanced ICT.
TWIN-CONTROL, a new simulation concept
The initiative addresses the design of an advanced machine tool simulation platform that brings together all the concepts influencing machining processes by combining advanced models.
This new concept will also take into account a number of elements such as predictive maintenance and energy efficiency that are essential in terms of increasing industrial productivity.
“Until now, theoretical simulation models analysed machine tools and machining processes independently, without any interaction between them. TWIN-CONTROL will bring together different simulation models designed to monitor machine operation and machining processes globally via only one platform”. “The project introduces a new simulation concept that unites the process and the machine”, says project co-ordinator Mikel Armendia at IK4-TEKNIKER.
The initiative has been designed to allow machine tool users to optimise their processes and upgrade productivity. The technology provided by TWIN-CONTROL will also enable users to improve machine operating behaviour, as data will be compiled in the form of a feedback to process parameters and improved results will be obtained continuously.
The expert also says “that it is a live feedback and continuous improvement process with regard to simulation and machine operation”.
The contribution of IK4-TEKNIKER
In addition to coordinating the project, the technology centre will focus its efforts on integrating the different TWIN-CONTROL simulation modules.
IK4-TEKNIKER will define all the details of this concept and develop new models to establish end-of-life parameters involving critical machine tool components in order to schedule maintenance actions more efficiently. A new machine tool status characterisation procedure will be designed and used on theoretical models for updating purposes.
“IK4-TEKNIKER provides a multi-disciplinary approach to machining processes that includes process knowledge, the machine tool proper as well as control parameters. This technology centre has extensive experience in terms of modelling and simulating the different concepts that influence machining process”, says Armendia.
All outcomes are to be validated by Renault and MASA in the automotive and aerospace business, two sectors that are highly strategic for the Basque and European economy. In addition, demonstrators will be installed to disseminate results at leading pilot centres specialising in research work focused on manufacturing processes: Factory 2050 of the AMRC at Sheffield University, the ETA-Factory at Darmstad University (Germany) and the Aeronautical CFA of the Basque Country.
In addition to the IK4-TEKNIKER technology centre, the Durango-based Gepro Systems aerospace engineering firm will also define requirements during the industrial validation stage.
The project’s international consortium also features other universities, industrial firms and research centres based in Spain, France, Germany, United Kingdom and Belgium.
The 36-month TWIN-CONTROL initiative began on October 1 and will be carried out by an alliance of eleven European partners.
The project has a total budget of 5.6 million Euros. Funding is to be supplied by the European Union under Horizon 2020, the European Research & Innovation Framework Programme.
This project has received funding from the European Union’s Horizon 2020 research and innovation programme under grant agreement nº 680725.