New technologies to facilitate person-robot collaborations in the area of industrial production
Tekniker has designed a robotic cell that performs bin picking operations and features three in-house AI solutions to improve natural person-robot collaborations and interactions. The solution will be on display at BIEMH 2024.
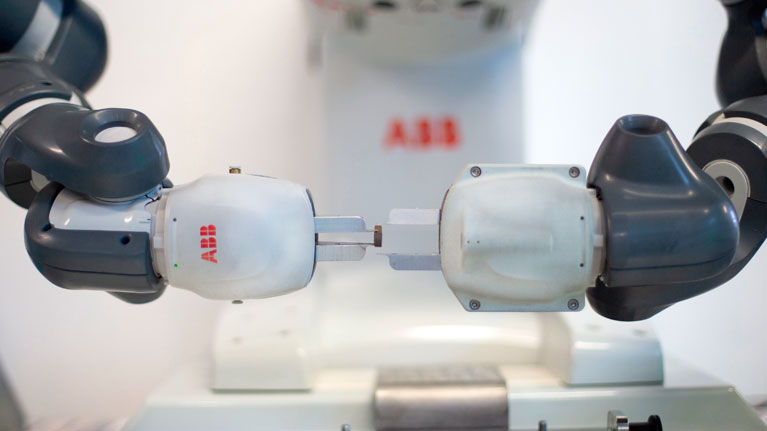
The growth and integration of new manufacturing technologies such as augmented reality, collaborative robotics and artificial intelligence and vision in industrial settings does not only make it possible to perform a wide range of operations but also makes them easily accessible to workers with different professional profiles.
A solution that plays a role in this new technological scenario is represented by bin picking systems used to meet industrial demands related to removing parts from containers or baskets. These systems incorporate artificial vision and robotics to identify parts so they can be handled.
The Tekniker technology centre, a member of the Basque Research and Technology Alliance (BRTA), is an organisation with an extensive amount of experience and knowledge related to these new production technologies. Its aim is to develop bin picking procedures by incorporating a layer of artificial intelligence (AI) that facilitates interactions between users and the robotic system.
Ultimately, the target is that users need not acquire any specific knowledge nor specialise in programming to interact with the system. Consequently, all kinds of professional profiles will be able to interact naturally without requiring any additional training.
The outcome of this process, to be displayed by Tekniker at the upcoming edition of the International Machine Tool Biennial (BIEMH), is a two-arm robotic cell that helps operators perform the highly demanding task of depositing parts accurately once picked up from another location where they have been previously placed haphazardly. An artificial vision system is also provided so the unit can decide how parts should be oriented depending on where they are to be left.
The robot will also feature a sophisticated artificial vision system that uses AI to monitor work done by operators to adapt to their pace. Quality control of all the operations carried out will also be performed and full traceability will be available.
Location, orientation and safety
The cell features three technologies fully developed by Tekniker that facilitate natural person-robot collaborations and interactions: a software called ‘SmartPicking’ to find parts, 2D software that ensures that parts are properly orientated and, finally, software to guarantee operator safety.
Eneko Ugalde, director of Autonomous and Intelligent Systems at Tekniker explains that “3D allows the robot to determine if any persons are present, the distance to them and slows the unit down if anybody is nearby”.
During the trade fair to be held at BEC, visitors will be provided with augmented reality goggles to view a simulation of the robot’s working environment, see how it moves and compare the robot physically with its projection on the device.
Ugalde also states that “in this instance, augmented reality provides a tool that virtualises real environments and operates with the digital twin of a production system in the form of a robot, although it does not require a physical environment, it is possible to programme the robot that will eventually be added on to the real system”.
Tekniker will showcase these technologies between June 3 & 7 on a stand at BIEMH2024 located on aisle E15, hall 1.