Industry 4.0, electroerosion, machine, IK4-TEKNIKER
IK4-TEKNIKER is developing a control system based on smart sensorics to increase process stability for a new family of machines made by the Basque manufacturer ONA.
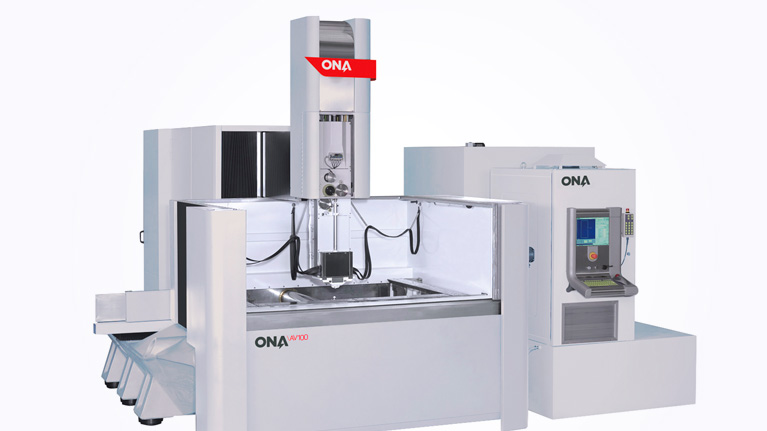
Intense competition in international markets requires the design of smart, flexible and accurate systems capable of increasing productivity and reducing costs.
In this scenario, the IK4-TEKNIKER technology centre is working with ONA, a manufacturer of electroerosion equipment, on the design of automatic control systems to develop a new range of highly stable machinery to deliver ultra-precise end results.
More specifically, the technological centre aims to create a new automatic process stability control system to optimise results by installing sensors that provide reliable information on machine operation parameters.
“This system is based on using multiple sensors and a self-calibration algorithm to achieve a stable, flexible, energy-efficient and environmentally-friendly electroerosion process. One of the most outstanding characteristics of this system is that as processes are optimised whilst manufacturing is underway, there are less rejects”, says the researcher in charge of the project at IK4-TEKNIKER, Eneko Gómez-Acedo.
To achieve this goal, technology centre researchers are developing a solution based on Industry 4.0 concepts to be fitted with automatic processes for the purpose of enhancing the process itself and exchanging information via the acquisition of signals delivered by multiple sensors.
This information system will be designed to provide a virtual, real-time simulation of the machine´s behaviour based on the data supplied by its sensors.
“The implementation of this new system will guarantee process stability and make it possible to reduce the cost of the parts to be made thanks to a minimal reject rate”, adds the researcher.
In addition to quality improvements, the fact that multiple data will be compiled during the process will allow valuable information to be obtained whilst manufacturing. Moreover, conclusions will be drawn, trends will be identified and traceability will be improved.
The role played by IK4-TEKNIKER
The technology centre is undertaking the task of developing the new automatic control system that will optimise process parameters related to variability and environmental factors.
The centre will develop new methodologies by performing experimental trials both before and after robust models are developed to achieve an effective real-time compensation of process variations.
In the technological field, moreover, IK4-TEKNIKER researchers will apply an innovative metrology process to perform automatic precision measurements to characterise the machine.
“Compared to the methods currently in use, the main advantages of this new one are that machine drift can be ascertained at multiple locations (instead of only at one spatial location) and measurement time is reduced thanks to an integrated measuring system with a high degree of automation. The method will make it possible to characterise machine and process stability", says Gómez-Acedo.
Likewise, researchers will be working on models to compensate process variability on a real time basis and study factors influencing the generation of thermal errors. These conditioning factors are to be tested on machines of different sizes.
The end results of this project will allow ONA to implement the new Industry 4.0 paradigm, whose ultimate goal consists in raising productivity.
It will be possible to use the new range of machines developed through this project in industrial sectors where high-precision parts are very demanded such as aeronautics, renewables, shipbuilding or machinery for civil works.