Roll-to-roll production system for cost-efficient manufacturing of extensive antimicrobial adhesive films
Roll-to-roll production system for cost-efficient manufacturing of extensive antimicrobial adhesive films.
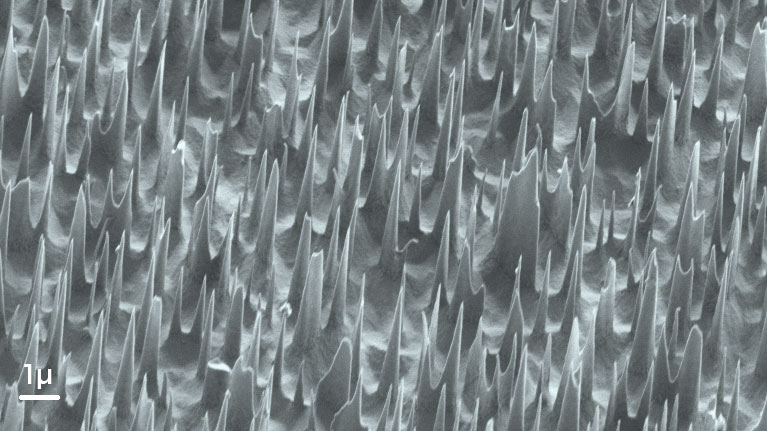
From bed rails, tray tables, telephones and alarm buttons to furnishings, door handles or taps: Hospitals are hotbeds for bacteria, which can lead to life-threatening infections in fragile patients.
The EU project “FLEXPOL” brings together a consortium of research and industry partners from Italy, Spain, Portu-gal, the United Kingdom and Germany to develop a pilot line for the manufacturing of cost-efficient antimicrobial adhesive films.
These films are applied to large-area surfaces around patients in order to reduce the risk of contamination. The combination of material and surface structure can kill various germs and inhibit bacterial growth with a targeted efficacy of 99 percent – this will not only ensure the health protection of both patients and medical staff but also yield a considerable economic benefit due to reduced expenditures for detergents and sanitizers.
The idea of the project is to apply these films to large areas such as walls and floors and thus extensively minimize a contamination with microbes.
This is achieved by specially developed nanostructures and polymer materials containing antimicrobial oil blends: Applying these structures to adhesive films in a roll-to-roll process makes it difficult for bacteria and fungal spores to cling to them as the structures mechanically damage the cell enve-lope and thus kill the pathogen. A promising effect that requires different steps, contribu-tions and collaborations from all the partners of the consortium.
The project commences with the compounding of the polypropylene material by the Italian company Celanese.
Softer S.p.A., which also contributes the rheological, thermal as well as mechanical characterization of the material. Throughout the project, Softer also advises in terms of material recycling and exploitation.
Concurrently, the Spanish company Naturality S.L. and researchers from the University of Alicante jointly work on the encapsulation of essential oils: Naturality takes over the actual oil extraction and develops concrete antimi-crobial blends against target bacteria; the University of Alicante provides their expertise by focusing on the design and characterization of the kinetics and mechanical properties of the essential oil release.
In a next step, Propagroup S.p.A. will take over the high-volume production of films by extruding the polypropylene material and the developed essential oil blends in a blow extrusion process. The granules are provided by partner Softer.
A crucial aspect of the project are the nanostructures containing the antimicrobial oil blends. These structures are collaboratively developed by the Spanish research institutes IK4-TEKNIKER and the Catalan Institute of Nanoscience and Nanotechnology (ICN2).
IK4-TEKNIKER has long-term experience in designing nanostructures and will contribute this expertise to the “FLEXPOL” project. Moreover, they will work on the thermal nano-imprint lithography, from batch to-batch-up to a continuous roll-to-roll protocol, as well as the manufacturing of large-area flexible stamps.
The Catalan Institute of Nanoscience and Nanotechnology (ICN2) will complement this with their fabrication techniques for hierar-chical topographies based on micro- and nanofeatures. Furthermore, it holds a patent for an in-line non-invasive measurement system and will also inspect the quality of the contin-uously produced film materials.
The German Fraunhofer Institute for Production Technology IPT, which is also the coordinator of the project, brings together the film material and nanostructures, the required tools as well as the necessary instruments for monitoring the product quality in a pilot line. In this context, the films are nanostructured by means of a roll-to-roll process that will be specially adapted to the requirements of the film structuring purposes.
The challenge of this production process is the seamless and extensive application of the antimicrobial surface structures to the film material.
Another challenge is the successful industrial transfer of these innovative adhesive films since the relevant materials, structures and processes have only been tested in laboratorios so far.
The “FLEXPOL” project will test the antimicrobial films in actual real-life medical environments, i.e. hospital settings and a nursing residence. The 3B’s research laboratories of the University of Minho in Portugal will characterize the antimicrobial behavior of the essential oils and the imprinted nanofeatures.
In parallel, the University Hospital Donostia in Spain will characterize and evaluate the films’ efficacy, durability, resistance against contamination and simultaneously assess selected cleaning and disinfection protocols.
Ultimately, Granta Design Ltd. (United Kingdom) will merge all information on materials, nanofeatures and their antimicrobial performance obtained throughout the project into a valid, reliable product documentation.
The EU project “FLEXPOL“ has a three-years duration, starting in January 2017 and con-cluding in December 2019. As a part of the funding program Horizon 2020, the project is supported by the European Commission with a budget of 5.17 million euros at a total budget of 5.68 million euros.