Smart robotised applications to handle very heavy loads
JATORMAN and IK4-TEKNIKER are developing a solution allowing heavy loads to be handled in a flexible and multi-functional manner that will also deliver a higher degree of accuracy and automation in the different processes to be carried out in order to reduce costs and shorten production times.
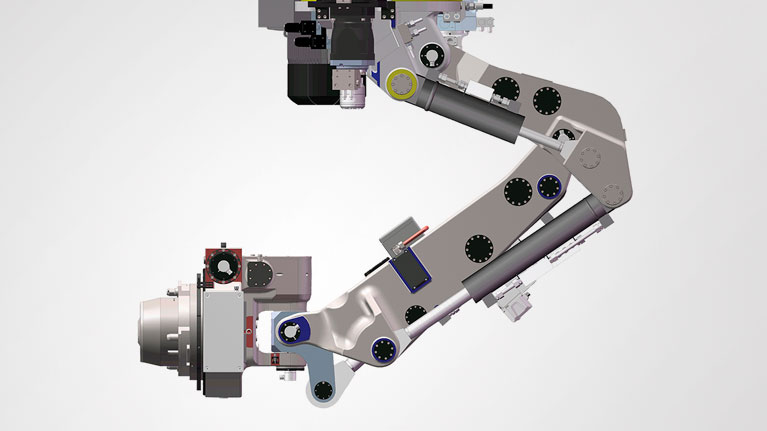
In the past, industrial companies resorted to manually guided machines in the form of gantry cranes or stationary positioners to handle all kinds of heavy parts involved in many assembly, machining or storage processes.
Current manufacturing and assembly processes, however, require that extremely heavy parts be moved accurately and safely. Sectors such as the renewables or automotive business require advanced technological solutions to handle heavy loads so that a number of operations can be carried with the load to shorten waiting times and save plant floor space.
In order to deal with this challenge, IK4-TEKNIKER has established a close cooperation JATORMAN, a company specialised in engineering solutions to develop a hydraulic robotic arm equipped with artificial vision and intelligence. This handling device, patented by JATORMAN, can handle maximum loads of three tons accurately and with total safety once it has been connected to the crane.
Firstly, a fully customised technical and economic feasibility study was carried out to look into specific automation requirements.
Secondly, most of the work connected to simulations, mechanical design and sizing was done. From the control engineering point of view, the design and development of the solution have posed a technological challenge. The robotic arm controls its various actuators autonomously to follow a trajectory established according to a given handling strategy.
Programming and control, based on a wireless interface, use a standard CNC language, a system that supplies several coordinate or "teaching" trajectories to adapt to a number of work scenarios and facilitate remote handling in aggressive or inaccessible environments.
The next step consisted in developing a pilot solution and commissioning a control system for the robotic arm; this also applied to the gantry crane whenever it ran in coordination with with the arm.
The robotic arm has been programmed to turn, swing, align, feed and handle all kinds of parts weighing up to three tons with absolute accuracy. It is also equipped with a system to exchange jaws automatically and adapt to any loads that are to be moved.
IK4-TEKNIKER has installed a sensor system on the robotic arm that provides a highly versatile solution to set up a person-robot collaborative environment backed by the technology centre´s expertise.
The solution enables safe loading and unloading operations involving heavy parts and toolings on machine tools, handling during assembly, die changes and palletising, especially whenever hazardous materials such as chemical, radioactive or incandescent materials have to be picked up and moved.
This development also features a so-called “parking space” to quickly disengage a gantry crane´s robotic arm so it can be allowed to work freely. By means of a simple exchange mechanism and the robotic arm itself it can travel through different working areas and different processes to reduce costs and shorten production times.
Once assembly work and fine-tuning operations have come to an end, IK4-TEKNIKER and JATORMAN will deliver a jointly developed internal training programme for the Navarre-based staff and future implementations.