New high-performance coatings based on solid lubricants that produce less environmental impacts
Tekniker participates in a research project aimed at replacing liquid lubrication with coatings based on solid lubricants for components manufactured by Azolgas and Shuton.
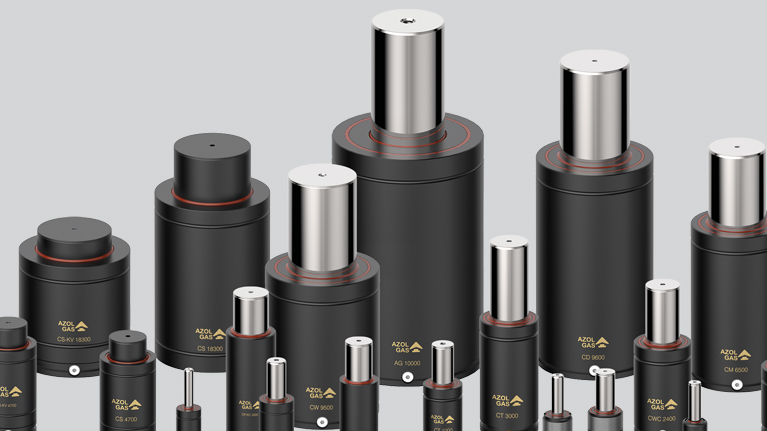
Tekniker is currently involved in Lubricoat, a European industrial project whose aim is to develop a new range of super-hard coatings based on solid lubricants to enhance performance and avoid the use of environmentally harmful liquid lubricants for industrial components made by Azolgas and Shuton.
These new coatings will be applied to nitrogen gas springs manufactured by Azolgas, the project leader, and to high-precision ball screws made by Shuton.
The Czech Technical University of Prague and the Fraunhofer IWS institute have been commissioned to develop and apply these coatings. Tekniker’s laboratories will analyse their performance in terms of friction, wear and corrosion and perform validation tasks.
Speeding up production
Gas springs manufactured by Azolgas are used for metal stamping in the automotive sector. The company has made a number of improvements in recent years to reduce the amount of heat generated inside the springs to meet the sector’s current demand in terms of speeding up production.
As explained by Elena Fuentes, a Tekniker researcher, by using solid lubrication instead of oil or grease “it has been possible to develop an innovative solution that will significantly speed up production and improve work patterns throughout a product’s entire life cycle”.
Shuton, on the other hand, designs and manufactures high-precision ball screws. Thanks to these new solid coatings it will be possible to extend screw life cycles and reduce maintenance work.
Moreover, the elimination of liquid lubricants will allow Shuton to reach out to other organisations operating in clean environments such as the food and pharmaceutical sectors where their use is not permitted.
Laboratory-tests and field trials
From a technical point of view, the ultimate goal of the Lubricoat project is to develop a new range of super hard coatings based on solid lubricants by combining molybdenum disulphide and carbon (MoS2-C) and applying innovative deposition techniques so the system can developed at an industrial scale.
Optimised coatings will laboratory-tested and end user companies will carry out field trials.
As regards gas springs, Tekniker will run all the tests required to identify surface treatments that offer the best tribological behaviour, produce less heat when in contact and reduce friction and wear.
As far as Shuton is concerned, coatings will be applied to nuts, screws and/or balls. Tekniker has also designed a new customised tribological configuration for validation purposed.
The technology centre will perform electrochemical corrosion and accelerated aging tests in salt spray booths.
The Tekniker researcher also says that "the success of the project will allow for the introduction of a lubrication technology that is cleaner and more ecological. It will also offer a wonderful opportunity to improve components at both companies to deliver high-added value products to access new, highly demanding markets".
Lubricoat is a research and development project under the umbrella of the Hazitek call with the M-ERA.NET seal whose aim is to improve the competitiveness of companies at a regional and European level. In addition to the previously mentioned organisations, the Technical University of Dresden (TUD) and AdvaMat, Theergarten-Pactec are also involved in the project.