Unique entity accredited by ENAC for calibrating CMMs using LASER TRACER technology
IK4-TEKNIKER has been accredited for calibrating large coordinate measuring machines using a sophisticated laser system.
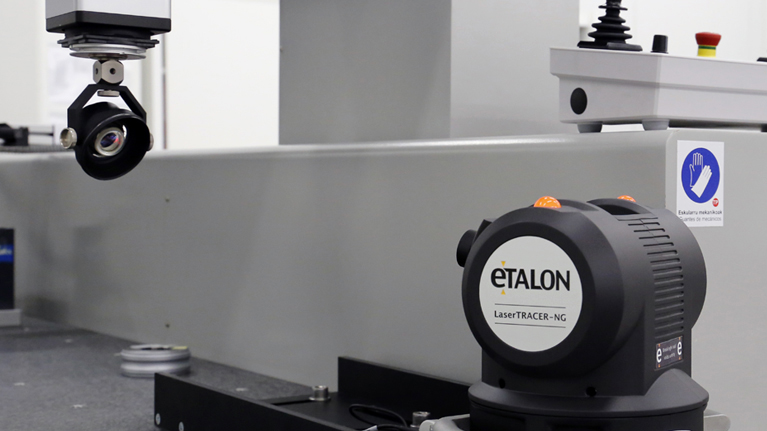
Companies need advanced measurement solutions that enable them to guarantee the reliability of key processes such as validating the quality of manufactured parts and obtaining data for analysis and critical decision making. Thus, in recent years manufacturers have used quality control equipment such as coordinate measuring machines (CMMs), high technological value equipment designed to calculate the geometric characteristics of an object. Despite their precision, these machines require exhaustive and costly periodic calibration to work correctly.
In this scenario, the IK4-TEKNIKER technology centre has been accredited by the National Accreditation Entity (ENAC) for calibrating medium-large CMMs (shaft length between 1,500 mm and 13,500 mm) using a sophisticated measuring system based on laser interferometry. The Basque centre has therefore become the only entity authorised in Spain to offer a calibration service using this technology, which replaces traditional physical calibration standards and significantly improves the time required compared to linear lasers.
The use of this technology offers a more efficient calibration solution for the large number of CMMs with a shaft greater than 1,500 mm that exist in Spain, which are presently calibrated using manual methods. The main problem of traditional calibration systems lies in the complexity of quickly and reliably using very long physical patterns.
Automated solution
Compared to manual methods, this system offers a fully automated solution that combines the most advanced laser interferometry technology, called LASER TRACER, which is designed by the German international company and benchmark in the metrology sector, ETALON AG, with data management software designed by IK4-TEKNIKER.
This solution consists of following a reflector located near the machine probe and measuring linear displacements. It thus performs a measurement process of 105 lengths spread over seven lines, offering two advantages over current processes. On the one hand, interferometric accuracy is maintained throughout the calibration process and, on the other, machine downtime (up to 6-8 hours) is considerably reduced.
The software created by IK4-TEKNIKER is connected via a computer to the CMM and the LASER TRACER measurement system and records the data obtained during calibration. Once all the checks have been carried out, the application generates reports that are compared with the performance data of the machine to detect possible mismatches, according to ISO 10360-2.
“Laser interferometry has made many advances with respect to the calibration methods used so far,” says Unai Mutilba, head of Inspection and Measurement at IK4-TEKNIKER. “The new system enables companies to reduce the downtime of their CMMs, verify larger machines, generate reports automatically and assign uncertainties for each of the 105 measurements that are made taking into account the temperature of the machine itself,” he concludes.
An open road in 2010
The accreditation granted to IK4-TEKNIKER is preceded by the introduction in 2010 by ISO (International Standards Organisation) of the possibility of using laser interferometry as a valid standard for calibrating CMMs, a circumstance that the technological centre has harnessed to develop a faster and more efficient and precise solution.
“This accreditation recognises the work undertaken in the centre and serves to generate greater confidence about the company’s activities in a key area of advanced manufacturing such as metrology,” added Mutilba.