Mantenimiento proactivo de maquinaria
El proyecto, desarrollado junto a Ibermática, propone una solución de monitorización y gestión de datos para conocer el estado de las máquinas herramienta, vigilar su evolución y recomendar acciones de mantenimiento predictivo para mejorar el rendimiento de los equipos.
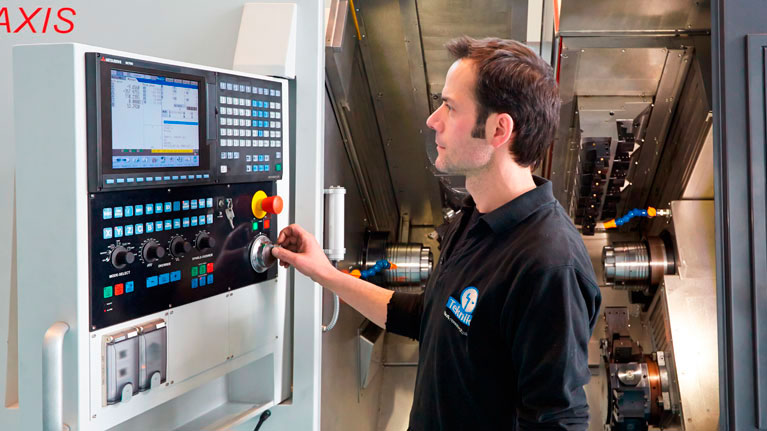
El sector de la máquina herramienta demanda cada vez más equipos de gran precisión y de alto valor añadido, pero también el desarrollo de sistemas que faciliten su propio mantenimiento, una tarea crítica e indispensable para mantener el propio funcionamiento de los equipos y, por lo tanto, su productividad.
La posibilidad que ofrecen las máquinas herramienta de recoger, transmitir y analizar una gran cantidad de datos, proporciona una información valiosa que ayuda a incrementar su productividad.
Captar datos del propio control de la máquina y de los sensores oportunos permite que se tenga, de manera continua y en tiempo real, información sobre el estado de los diferentes componentes de la máquina, sobre el estado de los procesos productivos, sobre los parámetros de calidad de las piezas fabricadas y sobre el entorno variable que rodea a la producción.
Mientras que los modelos predictivos basados en datos contribuyen a predecir el comportamiento de las máquinas para minimizar el riesgo de averías que provocan paradas de producción no programadas e importantes perjuicios económicos.
Además, se necesita una infraestructura que pueda captar, procesar, almacenar y explotar todos los datos, y correlacionarlos con el estado real de los componentes y las máquinas para conocer su comportamiento en uso y mejorar la capacidad de diagnóstico y predicción del sistema.
Monitorización basada en la condición y gestión de datos
IK4-TEKNIKER ha desarrollado junto a Ibermática, compañía de servicios en Tecnologías de la Información (TIC), una solución de monitorización y gestión de datos que tiene como objetivo conocer la salud de los componentes críticos de las máquinas herramienta y detectar situaciones de funcionamiento anómalo de manera temprana.
Esta herramienta está pensada para que, por un lado, los fabricantes de los equipos puedan prestar servicios de mantenimiento avanzado a sus clientes, y, por otro, para que los usuarios finales puedan comprobar que sus equipos funcionan de forma adecuada.
La solución se adecua a las capacidades de las empresas industriales en cuanto a conectividad e integración, y puede captar e interpretar toda la información que aporta valor añadido sobre el estado de salud de la máquina.
Para recoger señales de los controles y sensores, tanto internos como externos, IK4-TEKNIKER propone la realización de una serie de test de máquina, muy sencillos y rápidos, que permitan conocer el estado de la misma, mediante la evolución temporal de diferentes parámetros. Es lo que IK4-TEKNIKER denomina “Fingerprint de máquina”. De este modo, se puede comprobar cómo están funcionando las máquinas y hacer un seguimiento de la salud de los equipos de forma controlada.
Para la recogida de información se utiliza hardware capaz de conectarse a diferentes CNC de máquina herramienta, además de recoger información proveniente de la sensórica que se pueda instalar en máquina.
Este sistema permite conocer el estado de salud de la máquina y ayudar en la toma de decisiones relacionadas con la operación y el mantenimiento de la misma. Asimismo, permite adelantarse a la fabricación de piezas defectuosas, avanzando hacia la fabricación “cero defectos”, fundamental sobre todo en el caso de piezas de alto valor económico.
Pero no se trata sólo de recoger la información, los datos adquiridos son procesados para tener agregaciones y cálculos que faciliten su tratamiento posterior en la plataforma de gestión de estos datos.
Los datos post-procesados a través de los test de Fingerprint y los datos de operación, que aportan conocimiento del contexto de lo que pasa en la máquina herramienta, se envían a una plataforma preparada para su explotación. Esta plataforma capta, procesa, almacena y explota todos los datos, además de correlacionarlos con el estado real de los componentes y las máquinas para conocer su comportamiento en uso, mejorar la capacidad de diagnóstico y predicción del sistema, y en definitiva facilitar la toma de decisiones para mejorar el rendimiento de las máquinas herramienta.